Revolutionizing Manufacturing: The Ceramic 3D Printing Pioneers Reshaping Industry Frontiers
Manufacturing
2025-03-26 09:18:20Content
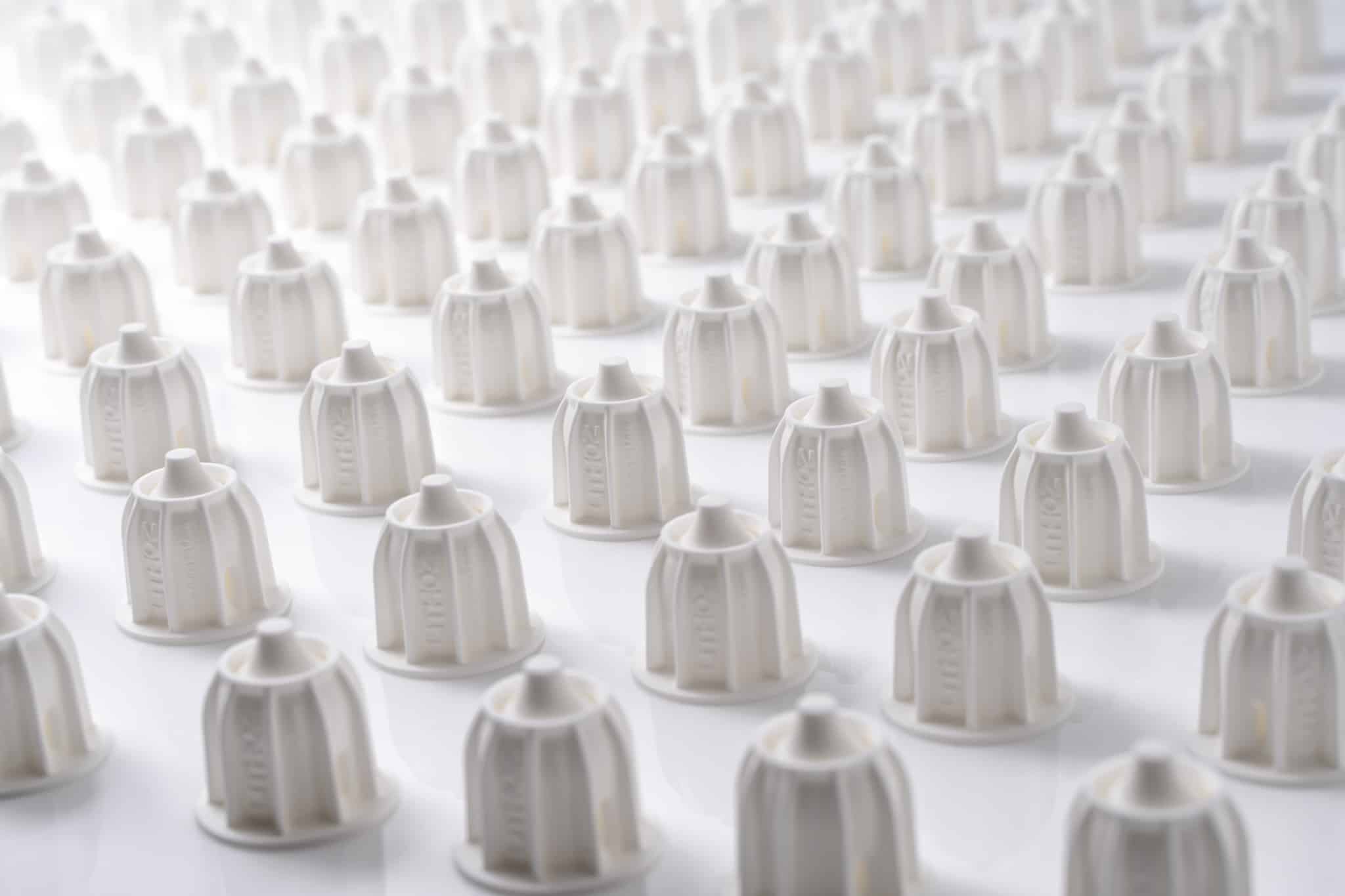
Revolutionizing Manufacturing: The Pioneers of Ceramic 3D Printing
In the cutting-edge world of advanced manufacturing, ceramic additive manufacturing is emerging as a game-changing technology that is transforming how we design, create, and innovate with technical ceramics. These innovative companies are pushing the boundaries of what's possible, delivering unprecedented precision, complexity, and performance across multiple industries.
Leading Innovators Reshaping Ceramic Manufacturing
At the forefront of this technological revolution are companies that are reimagining ceramic production through advanced 3D printing techniques. These trailblazers are not just creating components; they're engineering solutions that were previously impossible with traditional manufacturing methods.
Key Advantages of Ceramic Additive Manufacturing
- Unprecedented design flexibility
- Reduced material waste
- Complex geometries impossible with conventional methods
- Faster prototyping and production cycles
From aerospace and medical devices to electronics and industrial applications, ceramic 3D printing is opening new frontiers of innovation. Companies are developing specialized techniques that enable the creation of intricate ceramic parts with exceptional precision, strength, and thermal resistance.
The Future of Technical Ceramics
As research continues and technologies advance, we can expect even more groundbreaking developments in ceramic additive manufacturing. These innovations promise to revolutionize industries by providing lighter, stronger, and more sophisticated ceramic components that were once thought impossible to produce.
The journey of ceramic 3D printing is just beginning, and the potential seems limitless. Companies investing in this technology are not just manufacturing components—they're crafting the future of materials engineering.
Revolutionizing Manufacturing: The Ceramic 3D Printing Frontier
In the rapidly evolving landscape of advanced manufacturing, ceramic additive manufacturing stands as a transformative technology that is reshaping how industries approach complex component production. This groundbreaking field represents a convergence of materials science, engineering precision, and innovative technological capabilities that promise to redefine manufacturing paradigms across multiple sectors.Unleashing Unprecedented Potential: Ceramic 3D Printing's Industrial Revolution
The Technological Metamorphosis of Ceramic Manufacturing
Ceramic additive manufacturing represents a quantum leap beyond traditional manufacturing methodologies. Unlike conventional production techniques that rely on subtractive processes, this revolutionary approach enables engineers and designers to create intricate, geometrically complex ceramic components with unprecedented precision. The technology leverages advanced digital modeling and layer-by-layer fabrication techniques, allowing for unprecedented design freedom and material optimization. The fundamental breakthrough lies in the ability to produce ceramic structures with intricate internal geometries that were previously impossible to manufacture. Engineers can now design components with complex internal channels, lightweight lattice structures, and highly specialized surface textures that enhance performance characteristics.Pioneering Companies Transforming the Ceramic Landscape
Several innovative companies are driving the ceramic additive manufacturing revolution, each bringing unique technological approaches and specialized expertise. Companies like Lithoz, 3D Ceram, and Admatec are pushing the boundaries of what's possible in ceramic component production. Lithoz, for instance, has developed proprietary Lithography-based Ceramic Manufacturing (LCM) technology that enables the production of high-precision ceramic parts with exceptional surface quality and mechanical properties. Their approach allows for creating components with complex geometries that traditional manufacturing methods could never achieve.Critical Applications Across Diverse Industries
The potential applications of ceramic 3D printing span multiple high-performance sectors. In aerospace, lightweight yet incredibly robust ceramic components can significantly reduce aircraft weight while maintaining structural integrity. Medical industries are exploring patient-specific ceramic implants with customized geometries that perfectly match individual anatomical requirements. Advanced electronics represent another frontier, where ceramic additive manufacturing enables the creation of sophisticated heat-resistant and electrically insulating components. Semiconductor manufacturers are particularly excited about the potential for creating intricate ceramic substrates and packaging solutions that enhance device performance and reliability.Material Innovation and Performance Enhancement
Material science plays a crucial role in advancing ceramic additive manufacturing. Researchers are continuously developing new ceramic compositions that offer enhanced mechanical properties, improved thermal resistance, and superior electrical characteristics. Zirconia, alumina, and advanced ceramic composites are being refined to expand the technological capabilities of 3D printed ceramic components. The ability to precisely control material microstructures during the printing process allows for unprecedented material performance optimization. Engineers can now design components with gradient material properties, creating structures that seamlessly transition between different mechanical and thermal characteristics.Overcoming Technical Challenges
Despite its immense potential, ceramic additive manufacturing still faces significant technical challenges. The complex sintering processes, material shrinkage, and maintaining dimensional accuracy remain critical areas of ongoing research and development. Innovative companies are addressing these challenges through advanced computational modeling, sophisticated printing algorithms, and improved post-processing techniques. Machine learning and artificial intelligence are increasingly being employed to predict and mitigate potential manufacturing defects, driving continuous improvement in the technology.Economic and Sustainability Implications
Ceramic additive manufacturing offers substantial economic advantages by reducing material waste, enabling rapid prototyping, and facilitating on-demand production. The technology supports more sustainable manufacturing practices by minimizing raw material consumption and energy expenditure compared to traditional manufacturing methods. The potential for localized, distributed manufacturing could fundamentally transform global supply chains, allowing companies to produce complex ceramic components closer to the point of use, thereby reducing transportation costs and environmental impact.RELATED NEWS
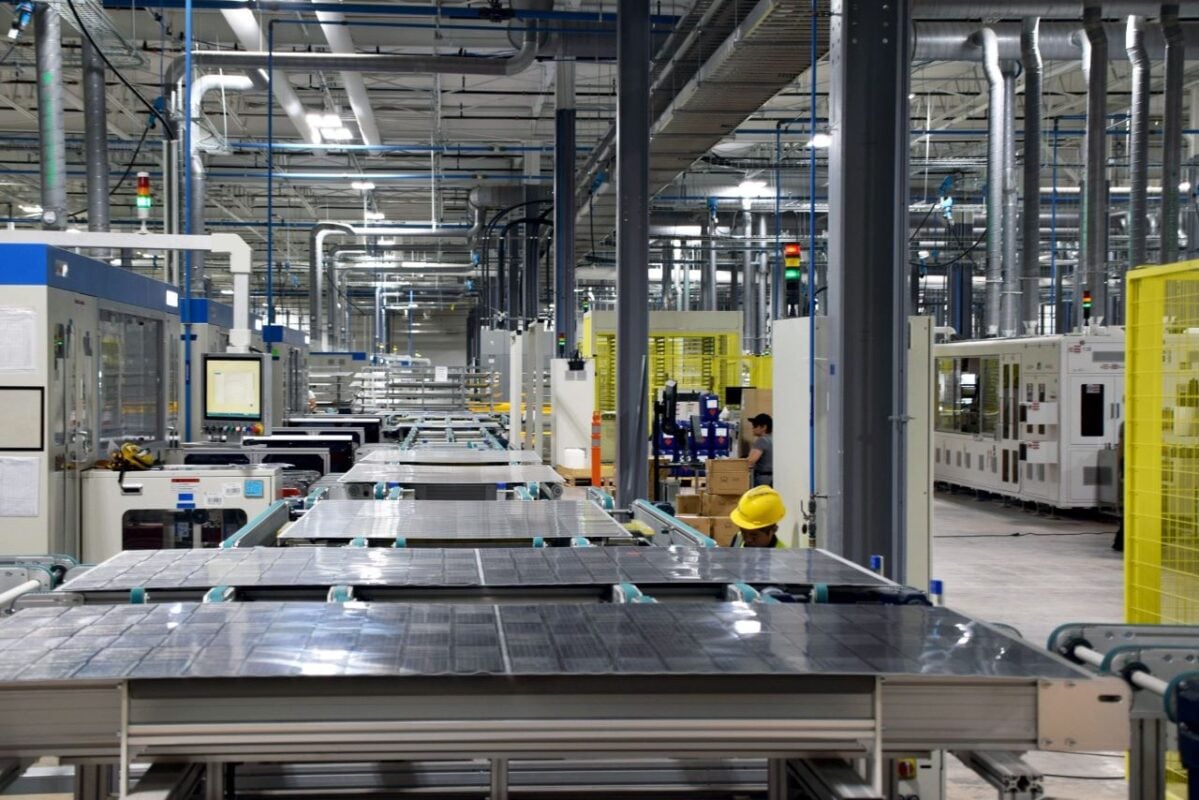
Solar Giant Canadian Solar Squeezed: Tariff Pressures Trigger Potential Manufacturing Exodus
Manufacturing Meltdown: Spain's Industrial Sector Hits Rough Patch in April Downturn
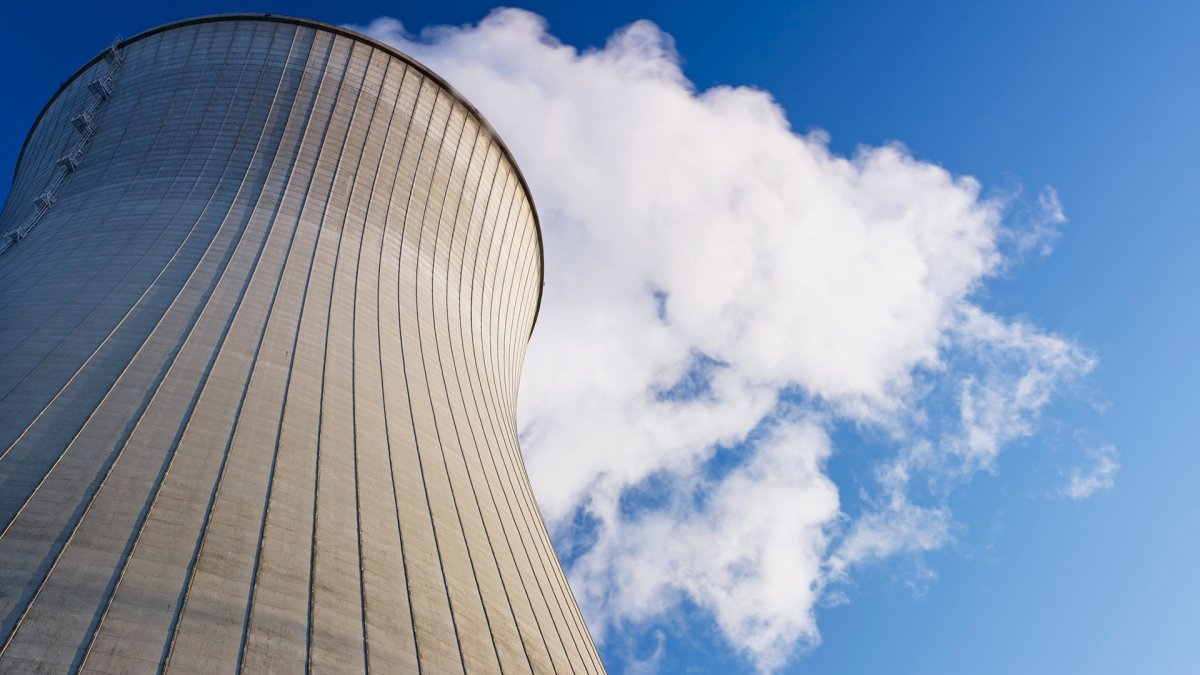