From Algorithms to Workforce: How AI is Transforming the Modern Worker
Manufacturing
2025-03-25 13:00:00Content
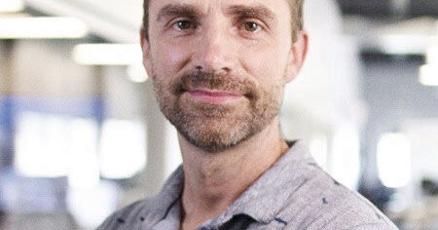
Revolutionizing Manufacturing: How AI-Powered Connected Worker Solutions Are Reshaping the Future of Work
In today's rapidly evolving industrial landscape, manufacturers are discovering a powerful secret to attracting top talent and boosting productivity: cutting-edge connected worker technologies powered by artificial intelligence. These innovative solutions are transforming traditional shop floors into dynamic, intelligent workspaces that speak directly to the next generation of workers.
Imagine a workplace where technology seamlessly bridges the gap between human expertise and digital intelligence. Connected worker platforms are doing exactly that, empowering employees with real-time insights, intuitive interfaces, and smart tools that make complex tasks more manageable and engaging.
Key Benefits of Connected Worker Solutions:
- Enhanced workplace collaboration
- Improved safety and training
- Real-time performance tracking
- Simplified knowledge transfer
- Attractive work environment for tech-savvy professionals
By embracing AI-driven connected worker technologies, manufacturers are not just upgrading their equipment—they're reimagining the entire employee experience. These solutions create an environment that resonates with younger workers who seek meaningful, technology-enhanced work opportunities.
The future of manufacturing is here, and it's more human-centric and intelligent than ever before.
Revolutionizing Manufacturing: How Artificial Intelligence Empowers the Next-Generation Workforce
In the rapidly evolving landscape of industrial innovation, manufacturers are facing unprecedented challenges in workforce engagement, technological integration, and operational efficiency. The convergence of artificial intelligence and human expertise is creating a transformative paradigm that promises to reshape the traditional manufacturing ecosystem, offering unprecedented opportunities for growth, skill development, and workplace modernization.Bridging Technology and Human Potential: The Future of Smart Manufacturing
The Digital Transformation of Manufacturing Workspaces
Modern manufacturing environments are undergoing a radical metamorphosis, driven by the seamless integration of artificial intelligence and connected worker technologies. Unlike traditional manufacturing models that relied heavily on manual labor and fragmented communication systems, today's smart factories are creating intelligent, responsive ecosystems that amplify human capabilities. Advanced AI-powered platforms are enabling real-time data collection, predictive maintenance, and dynamic workflow optimization. These technologies don't replace human workers but instead augment their skills, providing intuitive interfaces and intelligent insights that transform complex operational challenges into manageable, strategic opportunities.Connected Worker Solutions: Empowering the Next Generation
The emerging workforce, predominantly composed of digital-native millennials and Generation Z professionals, demands more than traditional employment models. They seek meaningful engagement, continuous learning opportunities, and technologically advanced work environments that challenge and inspire them. Connected worker solutions represent a groundbreaking approach to workforce development. By leveraging artificial intelligence, augmented reality, and sophisticated communication tools, manufacturers can create immersive learning experiences that attract, retain, and develop top talent. These platforms provide personalized training modules, real-time performance feedback, and collaborative problem-solving environments that resonate with tech-savvy professionals.Artificial Intelligence as a Collaborative Partner
Contrary to dystopian narratives about AI replacing human workers, contemporary research demonstrates that intelligent systems are most effective when designed as collaborative partners. Machine learning algorithms can process vast amounts of data, identify complex patterns, and generate actionable insights, while human workers contribute critical thinking, creativity, and nuanced decision-making capabilities. Advanced AI systems can now predict equipment failures, optimize production schedules, and provide contextual guidance to workers in real-time. This symbiotic relationship between human expertise and machine intelligence creates a more adaptive, resilient, and efficient manufacturing environment.Skill Development and Continuous Learning
The integration of AI-driven technologies fundamentally transforms workforce development strategies. Traditional training models are being replaced by dynamic, personalized learning experiences that adapt to individual worker's skills, learning styles, and career aspirations. Intelligent training platforms can analyze individual performance metrics, identify skill gaps, and recommend targeted learning interventions. This approach ensures that workers remain competitive, adaptable, and continuously evolving in a rapidly changing technological landscape.Economic and Competitive Advantages
Manufacturers who successfully implement connected worker solutions and AI technologies gain significant competitive advantages. These innovations reduce operational costs, minimize human error, accelerate training processes, and create more engaging work environments. By investing in intelligent workforce technologies, companies can attract top talent, improve operational efficiency, and position themselves as forward-thinking leaders in an increasingly digital global marketplace. The economic potential of these technologies extends far beyond immediate productivity gains, representing a fundamental reimagining of industrial workforce management.RELATED NEWS
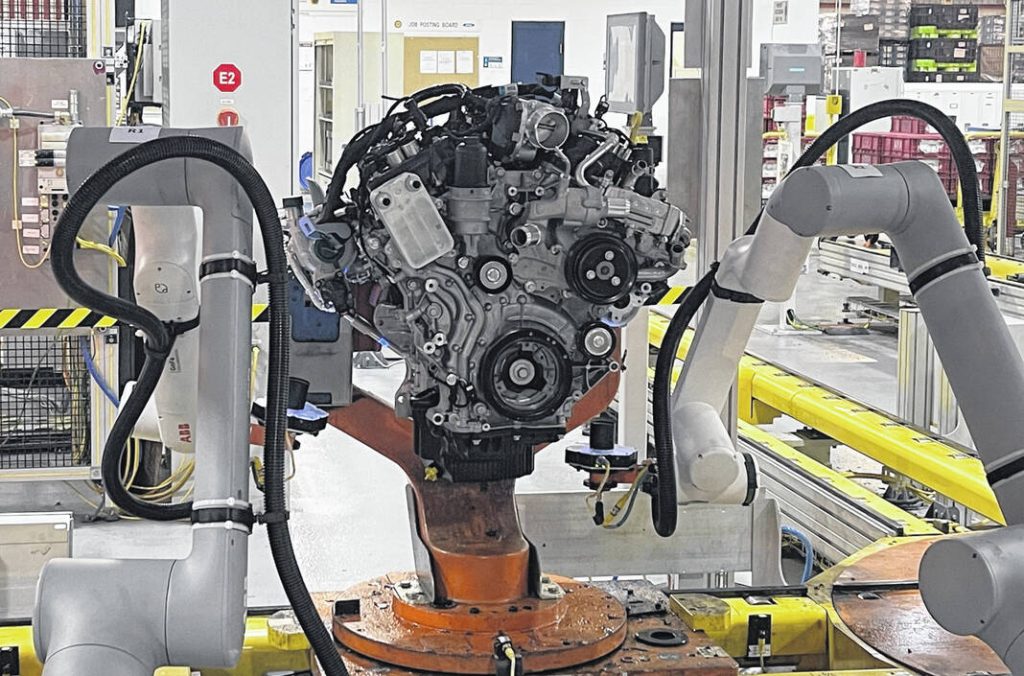
Resilient Factories: How Manufacturing Titans Are Reinventing Themselves in Challenging Times
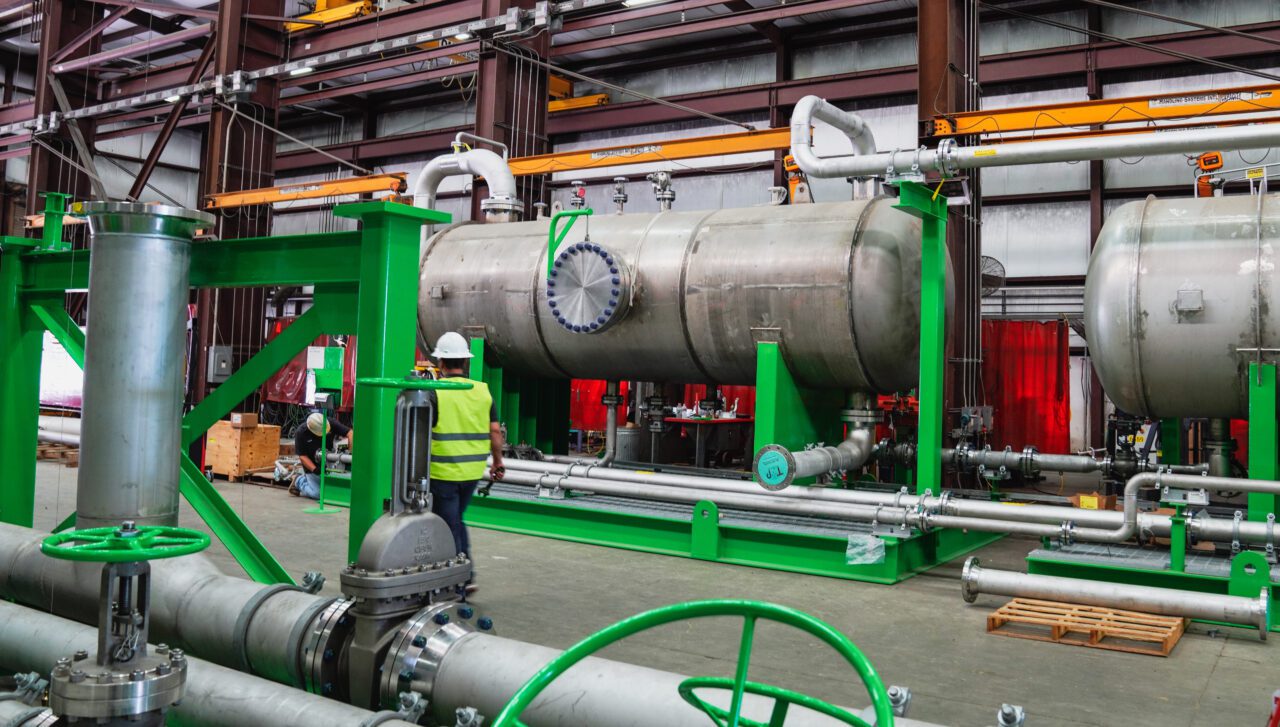