Manufacturing Boost: Sabhya Technologies Joins Forces with Cetec ERP to Empower Small Business Innovation
Manufacturing
2025-03-21 13:00:00Content
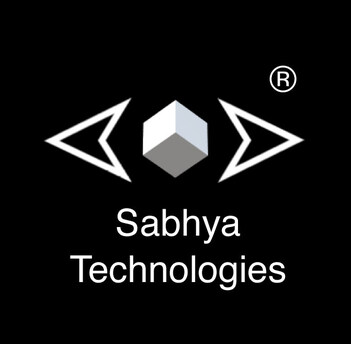
Streamlining Success: How Small Manufacturing Businesses Can Overcome Operational Challenges
Running a small manufacturing business is no small feat. Entrepreneurs and managers often find themselves caught in a complex web of operational hurdles—wrestling with fragmented systems, drowning in paper-based documentation, and struggling to maintain efficiency.
The Common Pain Points
- Disconnected software and tracking systems
- Time-consuming manual data entry
- Difficulty tracking production workflows
- Inefficient communication between departments
Breaking Through Operational Barriers
Modern manufacturing demands smart, integrated solutions that can transform these challenges into opportunities for growth. By embracing digital transformation and implementing streamlined management tools, small manufacturers can:
- Centralize data management
- Improve real-time tracking
- Enhance operational visibility
- Reduce administrative overhead
The key is finding scalable, user-friendly technologies that adapt to your unique business needs without overwhelming your team.
Revolutionizing Small Manufacturing: The Digital Transformation Imperative
In the rapidly evolving landscape of modern manufacturing, small businesses face unprecedented challenges that demand innovative solutions. The traditional methods of manual data tracking, fragmented systems, and paper-based processes are quickly becoming obsolete, threatening the survival and competitiveness of enterprises that fail to adapt to the digital age.Unlock Your Manufacturing Potential: Transform Chaos into Competitive Advantage
The Digital Disruption in Manufacturing Ecosystem
Modern manufacturing is experiencing a seismic shift driven by technological innovation. Small businesses are no longer competing on a local scale but are thrust into a global marketplace where efficiency, precision, and real-time data management are critical survival skills. The traditional manufacturing approach, characterized by fragmented systems and manual record-keeping, is rapidly becoming a liability rather than an operational strategy. The complexity of modern manufacturing demands an integrated approach that seamlessly connects every aspect of production. Advanced technologies like Internet of Things (IoT), artificial intelligence, and cloud-based management systems are transforming how businesses track, analyze, and optimize their operations. These technologies are not just incremental improvements but fundamental reimaginings of manufacturing processes.Strategic Technology Integration for Operational Excellence
Implementing comprehensive digital solutions requires a holistic approach that goes beyond simple software adoption. Successful digital transformation involves a cultural shift within the organization, where technology is viewed as a strategic enabler rather than a mere operational tool. Small manufacturers must develop a robust digital strategy that aligns technological investments with core business objectives. The journey begins with a comprehensive audit of existing systems, identifying bottlenecks, inefficiencies, and opportunities for technological intervention. Cloud-based Enterprise Resource Planning (ERP) systems offer unprecedented visibility into operations, allowing real-time tracking of inventory, production schedules, and resource allocation. Machine learning algorithms can predict maintenance needs, reducing downtime and optimizing equipment performance.Data-Driven Decision Making: The New Competitive Frontier
In the era of big data, information has become the most valuable asset for manufacturing businesses. Advanced analytics platforms enable manufacturers to transform raw data into actionable insights, driving strategic decision-making. By implementing sophisticated data collection and analysis tools, small manufacturers can gain unprecedented visibility into their operations. Predictive analytics can forecast market trends, optimize supply chain management, and identify potential risks before they materialize. Machine learning algorithms can analyze historical production data to recommend process improvements, resource allocation strategies, and potential areas of innovation. This data-driven approach transforms manufacturing from a reactive to a proactive discipline.Cybersecurity and Digital Resilience
As manufacturing becomes increasingly digital, robust cybersecurity measures become paramount. Small businesses must invest in comprehensive security frameworks that protect sensitive operational data, intellectual property, and customer information. This involves implementing multi-layered security protocols, regular system audits, and continuous employee training on digital safety practices. The potential risks of digital transformation are significant, but they pale in comparison to the risks of technological stagnation. Businesses that fail to modernize their systems will find themselves increasingly marginalized in a competitive global marketplace. Cybersecurity is not just a technical requirement but a strategic imperative that ensures business continuity and customer trust.Human Capital: The Critical Element of Digital Transformation
Technology alone cannot drive meaningful change. The most successful digital transformations are those that prioritize human capital, investing in employee training, cultural adaptation, and skill development. Small manufacturers must create learning environments that encourage technological literacy, innovation, and continuous improvement. Training programs should focus not just on technical skills but on developing a mindset of adaptability and continuous learning. Employees must be empowered to become active participants in the digital transformation process, understanding that technological innovation is a collaborative journey rather than a top-down mandate.RELATED NEWS
Manufacturing
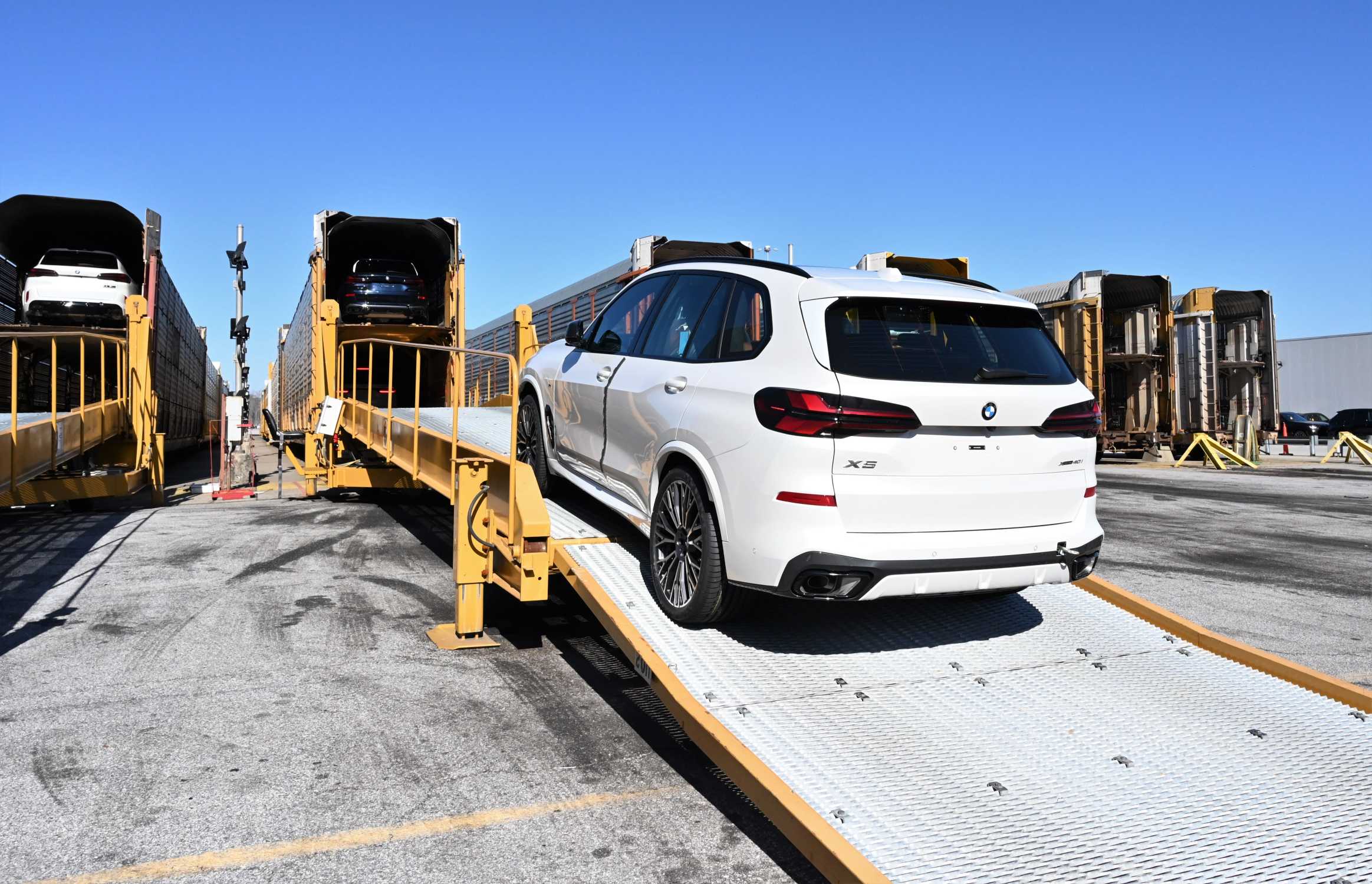
BMW's Global Triumph: $10.1 Billion Export Milestone Signals Electric Future
2025-03-01 08:00:00
Manufacturing
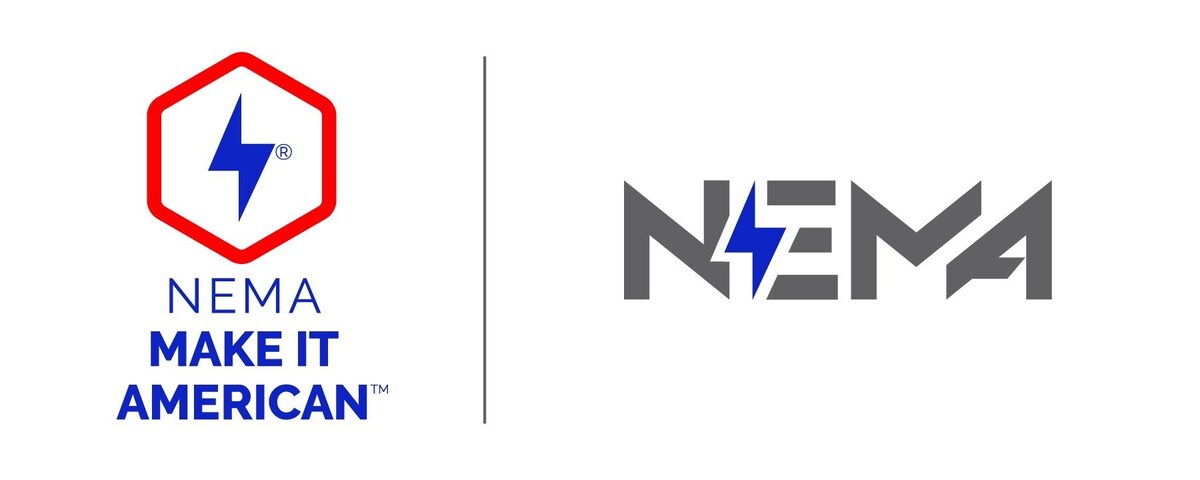
Made in America: NEMA's Bold New Certification Breathes Life into U.S. Manufacturing
2025-04-30 12:00:00
Manufacturing
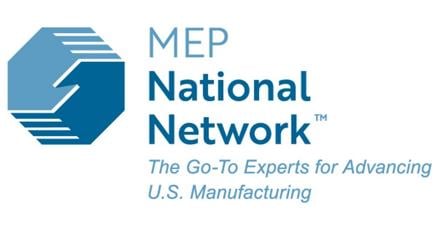
Manufacturing's Lifeline: Lawmakers Battle to Revive Critical Funding
2025-04-11 16:32:00