Beyond Pixels: How GM is Revolutionizing Pre-Production with Virtual Reality
Manufacturing
2025-03-11 10:30:00Content
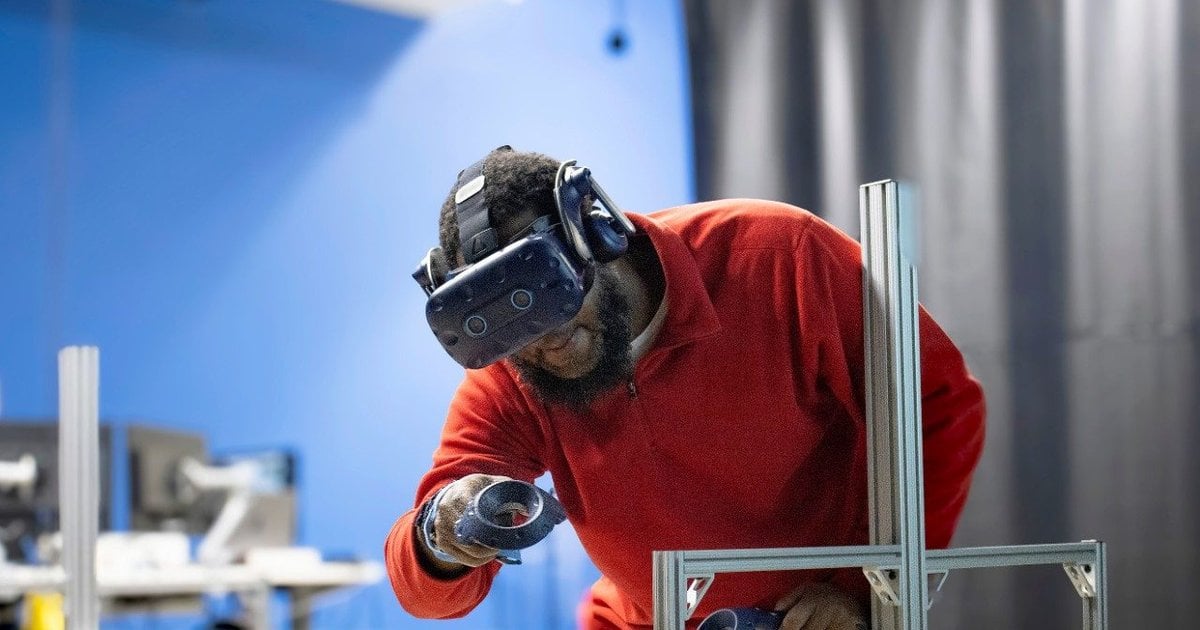
General Motors is revolutionizing automotive pre-production through cutting-edge virtual technology, setting a new standard for vehicle development and manufacturing excellence. By leveraging advanced digital simulation and modeling techniques, GM is transforming how vehicles are designed, tested, and refined before they ever touch the physical production line.
This innovative virtual-led strategy enables GM's engineering teams to dramatically enhance vehicle performance, reliability, and manufacturing efficiency. Through sophisticated computer simulations, engineers can now predict and resolve potential design challenges, optimize component interactions, and streamline the entire development process with unprecedented precision.
The approach allows GM to conduct extensive virtual testing across multiple scenarios, reducing physical prototype costs and accelerating time-to-market. By creating highly detailed digital models, the company can simulate complex engineering challenges, stress test vehicle systems, and validate design concepts with remarkable accuracy.
Key benefits of GM's virtual strategy include:
• Faster product development cycles
• Reduced engineering and prototyping expenses
• Enhanced vehicle performance and reliability
• More sustainable and efficient manufacturing processes
As automotive technology continues to evolve, GM's commitment to virtual-led innovation positions the company at the forefront of next-generation vehicle design and production.
Revolutionizing Automotive Design: General Motors' Virtual Reality Transformation
In the rapidly evolving landscape of automotive manufacturing, General Motors is pioneering a groundbreaking approach that merges cutting-edge technology with innovative design strategies. By leveraging virtual reality technologies, the automotive giant is redefining how vehicles are conceptualized, developed, and brought to life long before they ever touch an actual production line.Transforming Manufacturing Through Digital Innovation
Virtual Reality: The New Frontier of Automotive Engineering
General Motors has embarked on a transformative journey that transcends traditional manufacturing methodologies. By implementing advanced virtual reality technologies, the company has created an immersive digital environment where engineers and designers can simulate complex manufacturing processes with unprecedented precision. This digital approach allows teams to visualize and test vehicle configurations, identify potential challenges, and optimize design elements before physical prototypes are constructed. The virtual reality platforms enable GM's engineers to interact with intricate 3D models, manipulating components and exploring spatial relationships in ways that were previously impossible. By creating digital representations of manufacturing lines and vehicle structures, teams can conduct comprehensive assessments, reducing both time and resource expenditures associated with traditional development cycles.Precision Engineering Through Immersive Simulation
At the core of GM's strategy lies a sophisticated approach to digital simulation. Specialized VR operators like Dwaine Carswell utilize advanced technological tools to recreate entire manufacturing scenarios. Using unique reference points such as "ballerina bars" - metal frames that mimic vehicle structures - engineers can meticulously analyze seat installations, structural integrity, and potential manufacturing challenges. These immersive simulations provide multiple layers of insight. Engineers can rotate, zoom, and interact with virtual components, identifying potential design conflicts or ergonomic issues that might be overlooked in traditional 2D design processes. The level of detail achievable through these virtual environments allows for unprecedented precision in automotive engineering.Efficiency and Cost Reduction Through Digital Prototyping
The implementation of virtual reality technologies represents more than just a technological advancement; it's a fundamental reimagining of automotive product development. By conducting extensive digital testing and simulation, General Motors can significantly reduce physical prototype requirements, leading to substantial cost savings and accelerated development timelines. Each virtual simulation eliminates multiple stages of traditional prototyping, allowing engineers to rapidly iterate designs and resolve potential manufacturing challenges. The ability to make instantaneous modifications in a digital environment dramatically reduces the time and financial investments typically associated with automotive design and production.Collaborative Innovation in a Digital Ecosystem
General Motors' approach extends beyond individual technological capabilities, creating a collaborative digital ecosystem where engineers, designers, and manufacturing experts can seamlessly interact. Virtual reality platforms enable real-time communication and design modifications, breaking down traditional departmental barriers and fostering a more integrated approach to automotive development. This collaborative model allows for rapid knowledge sharing and collective problem-solving. Teams across different geographical locations can simultaneously explore and contribute to design iterations, creating a more dynamic and responsive product development process.Future-Proofing Automotive Manufacturing
By investing heavily in virtual reality technologies, General Motors is positioning itself at the forefront of automotive innovation. The company's commitment to digital transformation signals a broader industry trend towards more technologically sophisticated design and manufacturing approaches. The integration of artificial intelligence, machine learning, and advanced simulation technologies promises to further revolutionize how vehicles are conceived, designed, and brought to market. General Motors' current strategies lay the groundwork for a more agile, efficient, and innovative automotive manufacturing landscape.RELATED NEWS
Manufacturing
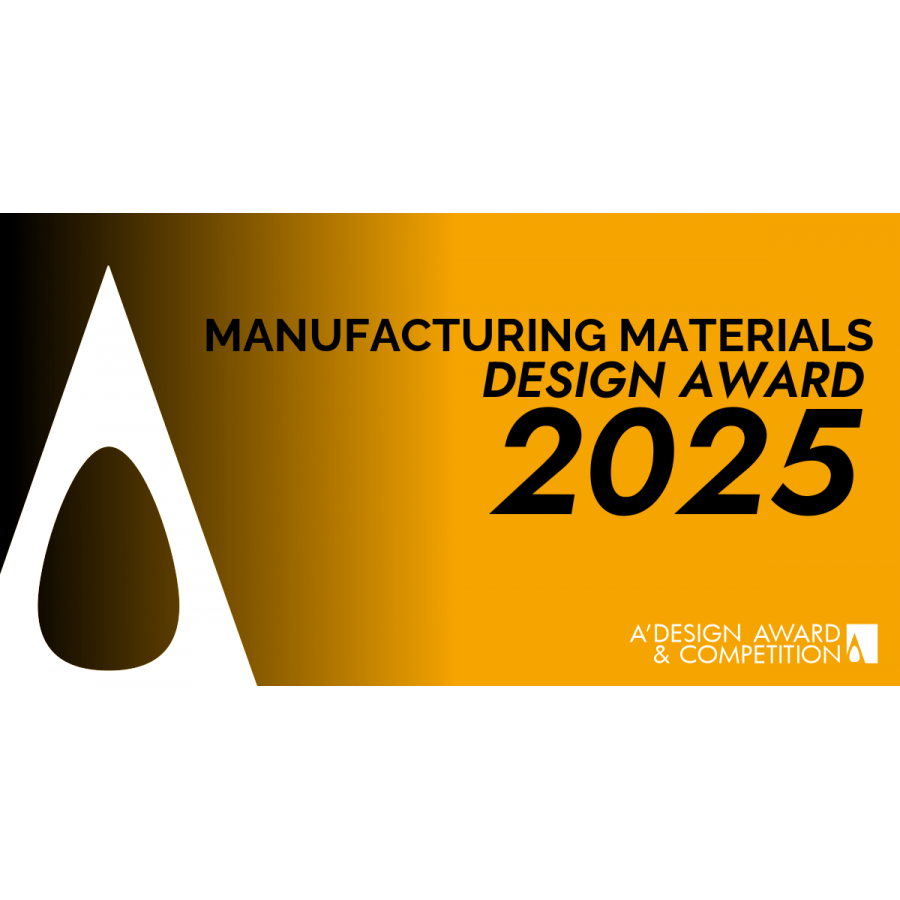
Innovators Triumph: A' Design Awards Unveil Groundbreaking Manufacturing Excellence for 2024
2025-03-14 07:47:37
Manufacturing
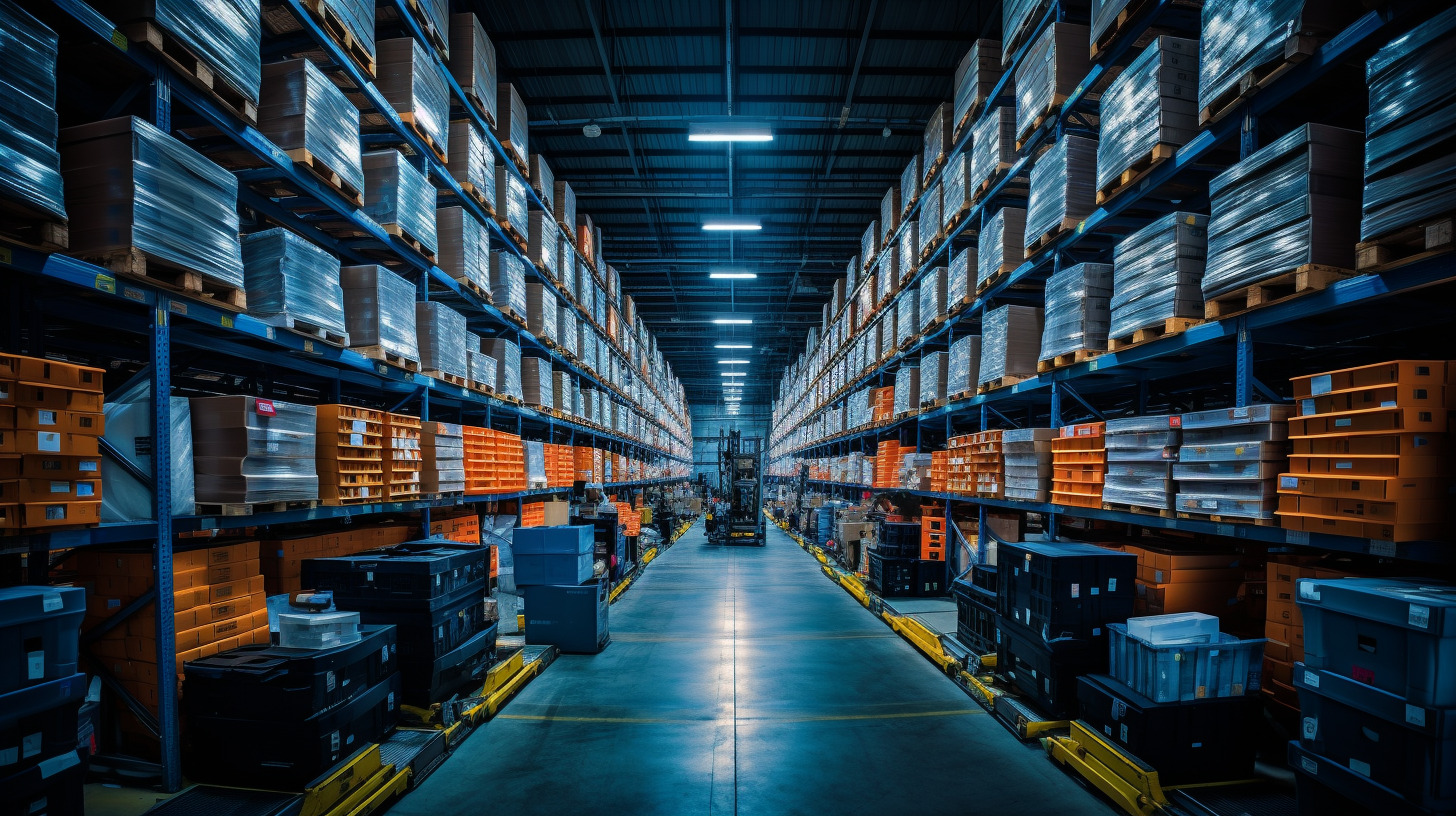
Wall Street's Hidden Gems: 15 Manufacturing Minnows Catching Hedge Fund Attention
2025-04-27 14:36:51
Manufacturing
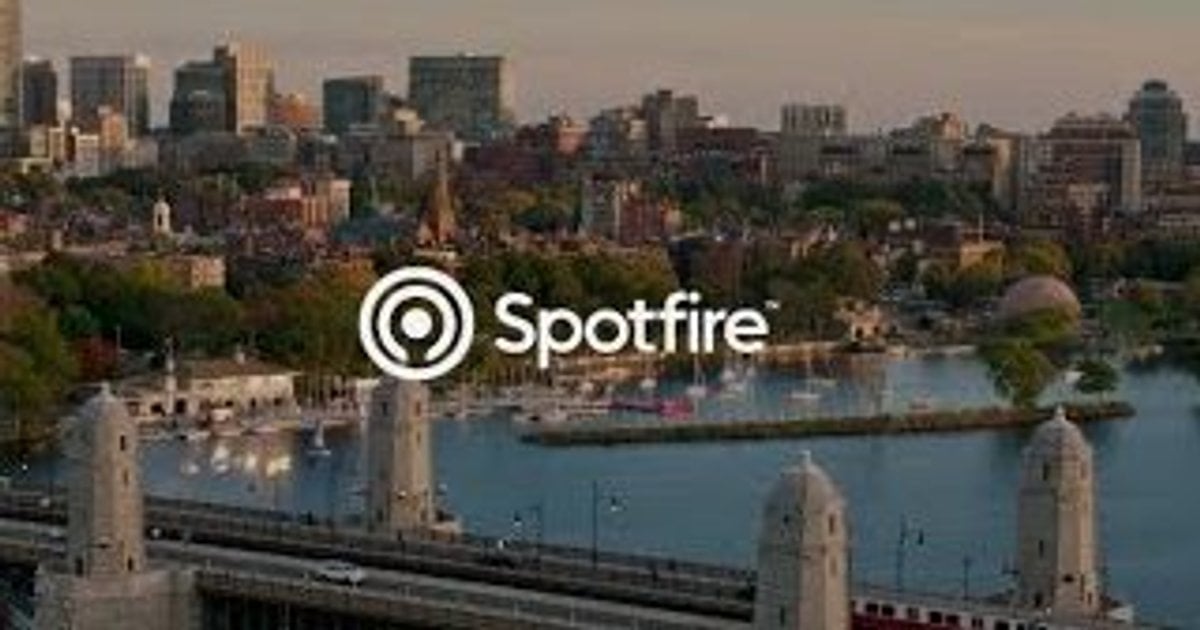
Breaking: Spotfire's Visual Data Science Revolutionizes Innovation Landscape
2025-05-01 10:47:37