Errors & Omissions: The Unexpected Guardian of America's Manufacturing Comeback
Manufacturing
2025-04-11 15:36:55Content
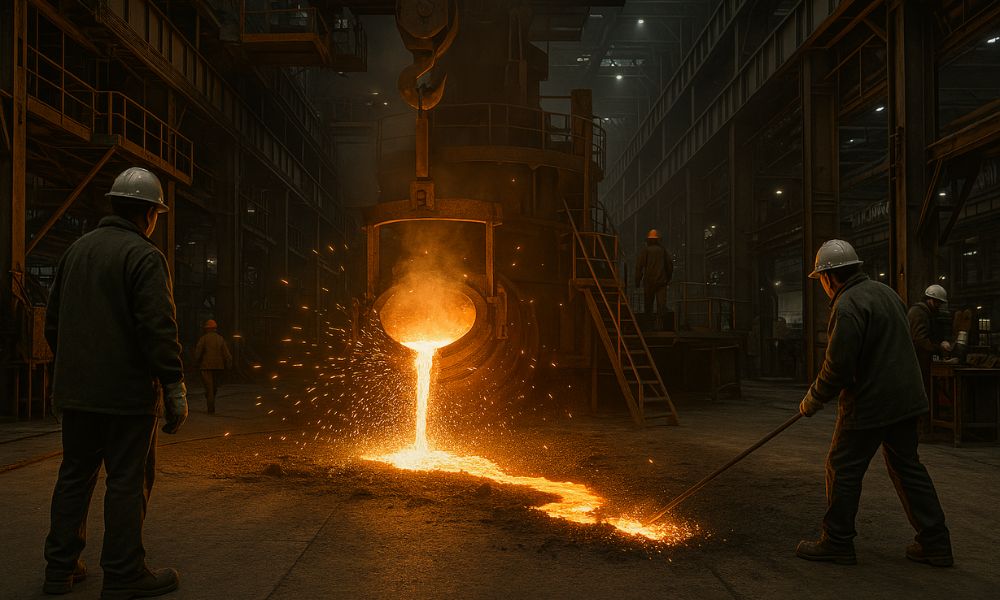
In the complex world of manufacturing, a single misstep can transform a promising production run into a costly nightmare. Beyond the raw material expenses, manufacturing errors can trigger a cascade of financial and operational challenges that far exceed initial material investments.
Precision is the cornerstone of successful manufacturing. Even minor deviations from design specifications can lead to significant quality control issues, product recalls, and substantial financial losses. These mistakes aren't just about wasted resources; they represent potential damage to a company's reputation, customer trust, and long-term market competitiveness.
Consider the ripple effects of a manufacturing error: rejected batches, rework costs, delayed shipments, and potential contractual penalties. What might seem like a small technical oversight can quickly escalate into a complex and expensive problem. Smart manufacturers invest in rigorous quality control processes, advanced training, and cutting-edge technologies to minimize these risks.
The true cost of manufacturing mistakes extends far beyond simple material expenses. It encompasses lost productivity, reduced efficiency, increased labor costs, and potential long-term brand reputation damage. In today's competitive global market, manufacturers cannot afford to be cavalier about precision and quality.
The Hidden Economic Tsunami: When Manufacturing Errors Devour Profits
In the intricate world of industrial production, a single misstep can transform a promising venture into a financial nightmare. Manufacturing represents the backbone of economic innovation, yet beneath its seemingly structured surface lies a complex landscape of potential errors that can silently erode a company's financial foundation.Unmasking the Silent Profit Killer in Industrial Production
The Microscopic Origins of Massive Financial Devastation
Manufacturing errors are not merely technical glitches but sophisticated economic disruptions that can cascade through entire production ecosystems. These seemingly minor deviations from precision standards can trigger exponential financial consequences that extend far beyond immediate material costs. Modern manufacturing environments demand microscopic attention to detail, where even the most infinitesimal deviation can trigger systemic failures. Advanced quality control mechanisms have evolved to detect potential errors, but the real challenge lies in understanding the intricate economic ripple effects. Each manufacturing mistake represents a potential breach in the delicate balance of production efficiency, potentially compromising product integrity, brand reputation, and long-term market positioning.Economic Anatomy of Manufacturing Mistakes
The financial impact of manufacturing errors transcends simple material replacement costs. When a production line experiences systematic mistakes, the economic repercussions can include increased labor expenses, extended production timelines, potential legal liabilities, and significant reputational damage. Companies operating in high-precision industries like aerospace, medical devices, and advanced electronics face exponentially higher stakes. Statistical analyses reveal that manufacturing errors can consume up to 20-30% of production budgets, a staggering figure that underscores the critical importance of implementing robust quality assurance protocols. These errors are not just financial drains but potential catalysts for comprehensive operational restructuring.Technological Interventions and Predictive Strategies
Contemporary manufacturing landscapes are increasingly leveraging artificial intelligence and machine learning algorithms to predict and prevent potential errors. These sophisticated technological interventions analyze historical production data, identifying subtle patterns that human observers might overlook. Predictive maintenance strategies now integrate advanced sensor technologies and real-time monitoring systems, enabling manufacturers to anticipate potential failures before they manifest. By transforming reactive approaches into proactive methodologies, companies can significantly mitigate the economic risks associated with manufacturing mistakes.Human Factor: Training and Cultural Transformation
While technological solutions play a crucial role, the human element remains paramount in preventing manufacturing errors. Comprehensive training programs that emphasize precision, accountability, and continuous learning can fundamentally reshape organizational cultures. Successful manufacturing environments cultivate a holistic approach where every team member understands their role in maintaining quality standards. This cultural transformation goes beyond traditional training models, embedding error prevention as a core organizational value rather than a peripheral consideration.Global Economic Implications
Manufacturing mistakes are not isolated incidents but potential systemic risks with global economic implications. In an interconnected global supply chain, a single error can disrupt multiple production networks, causing cascading economic consequences that extend across international boundaries. The economic resilience of manufacturing sectors depends on their ability to develop adaptive, intelligent systems that can rapidly identify, isolate, and rectify potential errors. This requires a multidisciplinary approach integrating engineering, data science, economic analysis, and organizational psychology.RELATED NEWS
Manufacturing
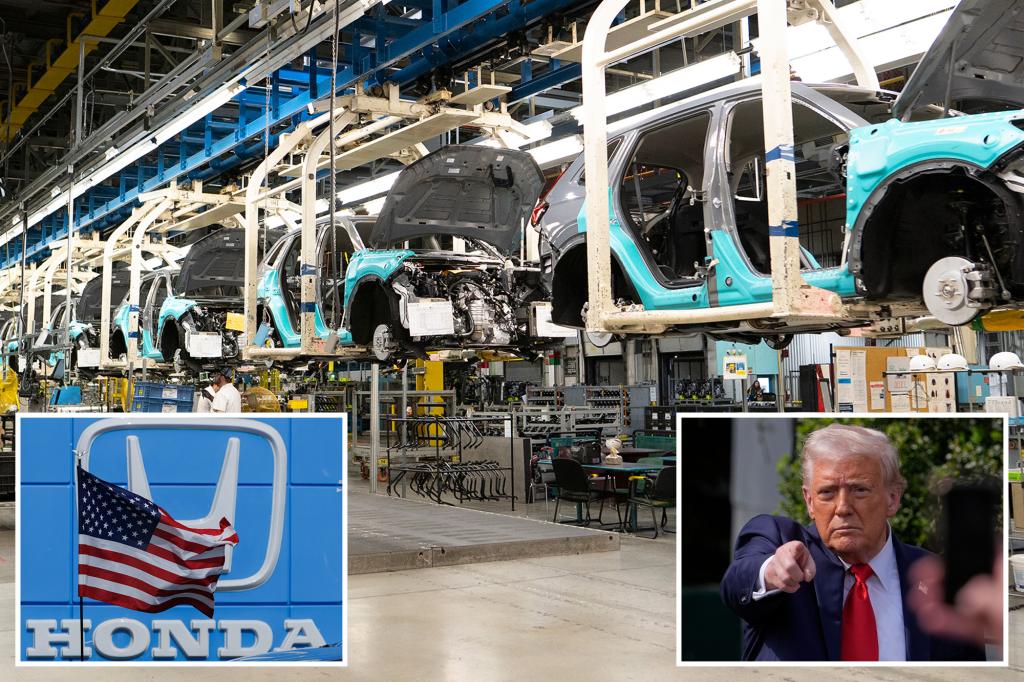
Honda's Bold Move: Revving Up US Manufacturing with Major Production Shift
2025-04-15 15:24:45
Manufacturing
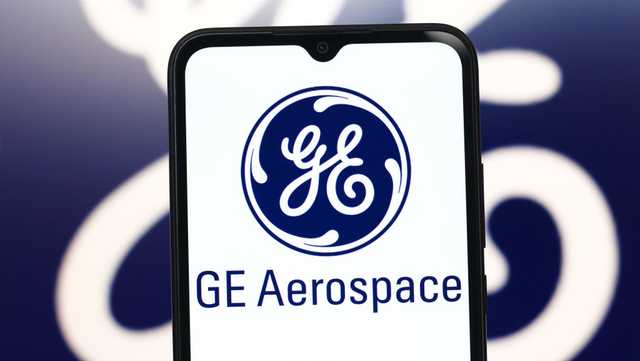
Powering Up the Heartland: GE Aerospace Drops $113M to Supercharge Cincinnati Manufacturing
2025-03-12 21:33:00
Manufacturing
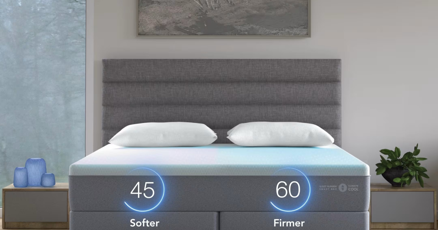
Local Innovator Triumphs: Irmo Company Clinches Top Spot in SC Manufacturing Showdown
2025-03-10 16:04:00