3D Printing Revolution: Breakthrough Technologies Reshaping Manufacturing Landscape in 2025
Manufacturing
2025-02-28 14:45:46Content
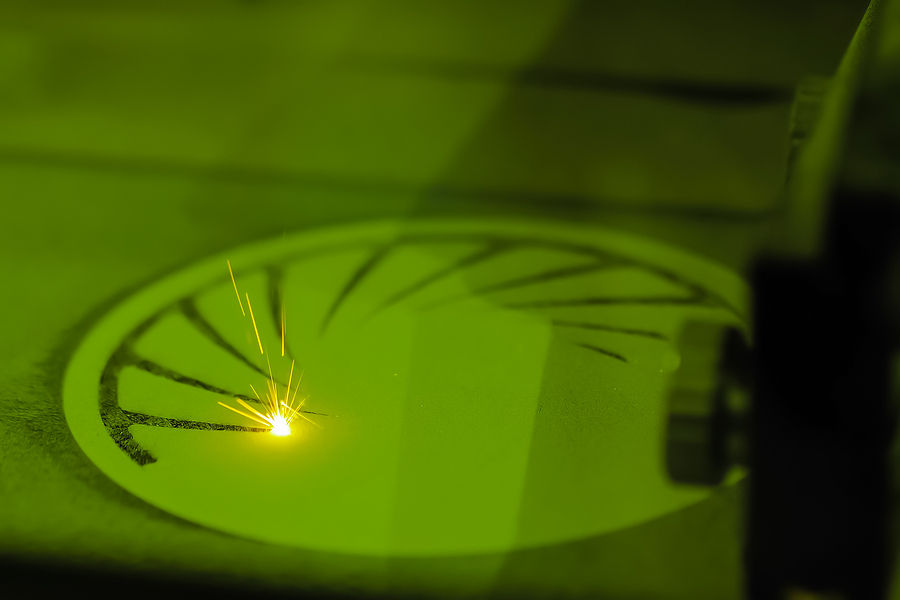
Revolutionizing 3D Printing: Powder Bed Fusion Meets Sustainability and Chess Innovation
In the cutting-edge world of additive manufacturing, powder bed fusion technology is pushing the boundaries of what's possible in 3D printing. Researchers and engineers are now achieving unprecedented levels of precision and efficiency, transforming how we approach complex manufacturing challenges.
The latest breakthrough comes from an innovative approach to optimizing printing parameters. By fine-tuning temperature controls, particle distribution, and laser scanning strategies, manufacturers can now create intricate components with remarkable speed and accuracy. This isn't just about technical prowess – it's about sustainability and pushing the limits of design.
Chess enthusiasts are particularly excited about these advancements. 3D printing now allows for creating custom chess sets with unprecedented detail and complexity. Imagine personalized chess pieces that are not just game components, but true works of art – each piece a testament to the precision of modern manufacturing techniques.
The environmental impact is equally impressive. Powder bed fusion technologies are becoming increasingly eco-friendly, reducing material waste and energy consumption. By optimizing printing parameters, manufacturers can now create complex parts with minimal material loss, representing a significant step towards more sustainable manufacturing processes.
From intricate chess pieces to complex engineering components, powder bed fusion is redefining what's possible in 3D printing. It's a perfect blend of technological innovation, artistic expression, and environmental consciousness – proving that cutting-edge manufacturing can be both precise and sustainable.
Revolutionizing Manufacturing: The Cutting-Edge World of Additive Manufacturing and Precision Engineering
In the rapidly evolving landscape of modern manufacturing, technological innovations are reshaping how we conceptualize, design, and produce complex components across multiple industries. The convergence of advanced materials science, computational modeling, and precision engineering has opened unprecedented frontiers in manufacturing capabilities, challenging traditional production methodologies and pushing the boundaries of what's possible in design and fabrication.Transforming Innovation: Where Precision Meets Possibility
The Quantum Leap in Powder Bed Fusion Technology
Powder bed fusion represents a groundbreaking approach to advanced manufacturing, fundamentally reimagining how intricate components are created. This sophisticated technique allows engineers and designers to transform digital blueprints into tangible, high-precision objects with remarkable complexity and structural integrity. By strategically deploying laser technologies, manufacturers can selectively melt powdered materials—ranging from metals to advanced polymers—creating components with unprecedented geometric intricacy and mechanical performance. The process involves meticulously layering microscopic material particles, which are precisely melted and consolidated using high-energy laser systems. Each layer represents a microscopic cross-section of the final design, enabling the creation of structures that would be impossible through conventional manufacturing techniques. This approach allows for unprecedented design freedom, enabling engineers to develop components with internal geometries, complex lattice structures, and optimized weight-to-strength ratios.Sustainability at the Forefront of Advanced Manufacturing
Modern additive manufacturing techniques are not just about technological prowess but also represent a significant stride towards sustainable production methodologies. Traditional subtractive manufacturing often generates substantial material waste, with significant portions of raw materials being cut away and discarded. In contrast, powder bed fusion technologies minimize waste by utilizing only the exact amount of material required for the specific component. Environmental considerations extend beyond material efficiency. The ability to produce lightweight, optimized components directly translates to reduced energy consumption in subsequent applications. For instance, aerospace and automotive industries can leverage these technologies to create components that are substantially lighter, leading to improved fuel efficiency and reduced carbon emissions throughout a product's lifecycle.Computational Simulation: The Invisible Engineering Powerhouse
Behind every successful additive manufacturing process lies an intricate world of computational simulation and predictive modeling. Advanced algorithms and sophisticated software platforms enable engineers to simulate and predict material behavior, thermal dynamics, and structural performance before physical production begins. These computational tools allow for unprecedented optimization, reducing prototype iterations and minimizing development costs. By creating virtual representations of complex manufacturing processes, engineers can anticipate potential challenges, optimize design parameters, and ensure superior final product quality. Machine learning and artificial intelligence are increasingly being integrated into these simulation frameworks, further enhancing predictive capabilities and reducing human error.Beyond Manufacturing: Interdisciplinary Applications
The implications of advanced additive manufacturing extend far beyond traditional industrial applications. Medical fields are witnessing revolutionary developments, with custom prosthetics, patient-specific surgical guides, and even bioprinted tissue structures becoming increasingly feasible. Architectural and construction industries are exploring large-scale 3D printing techniques for sustainable building solutions, while aerospace and defense sectors continue to push technological boundaries. The chess metaphor embedded in the original concept becomes particularly apt—each technological advancement represents a strategic move, carefully calculated and executed with precision. Just as a chess grandmaster anticipates multiple moves ahead, modern engineers are designing manufacturing processes that are several technological generations ahead of traditional approaches.RELATED NEWS
Manufacturing
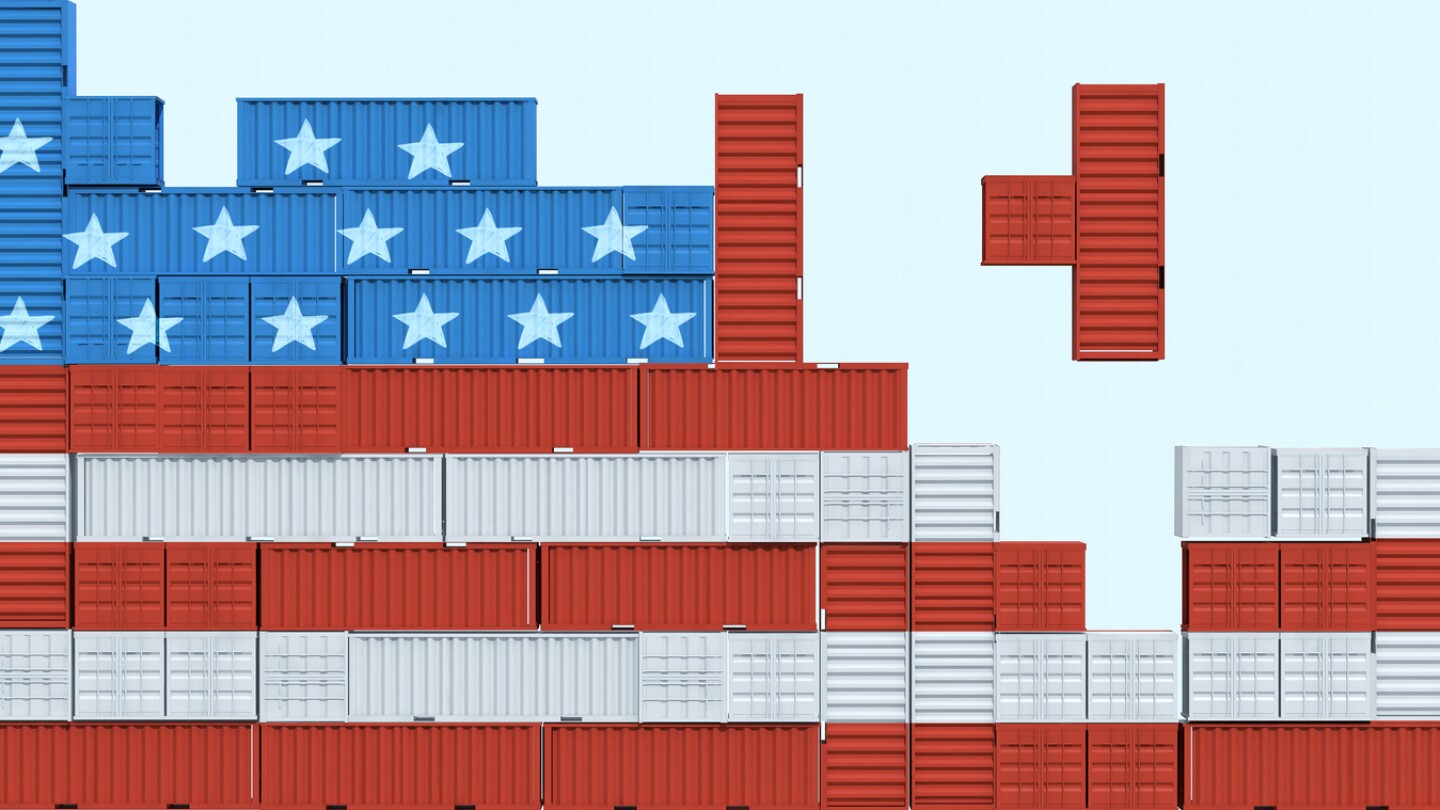
Pharma Giants Roche and Regeneron Double Down on US Production Amid Trade Tensions
2025-04-22 13:00:58
Manufacturing
Chip Giant TSMC Defies Trade Tensions: Massive $10.7B Q1 Windfall Despite US Tariff Challenges
2025-04-17 12:03:45
Manufacturing
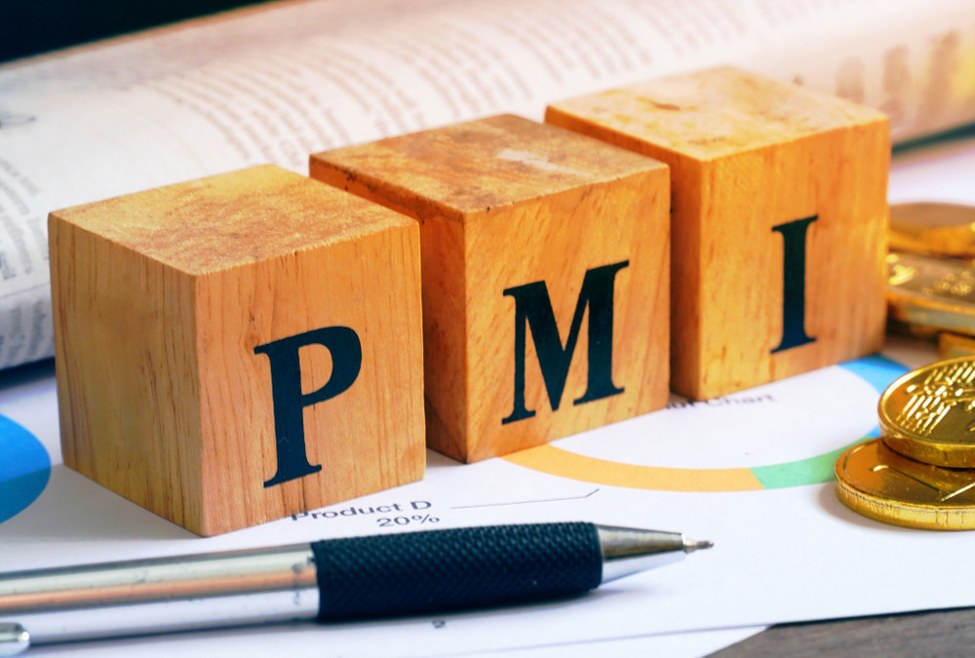
Manufacturing Momentum: Japan's Industrial Sector Shows Signs of Resilience with Surprise PMI Uptick
2025-03-03 00:38:09