Robots, Redesign, Revolution: How Smart Assembly is Transforming Manufacturing
Manufacturing
2025-04-01 13:00:00Content
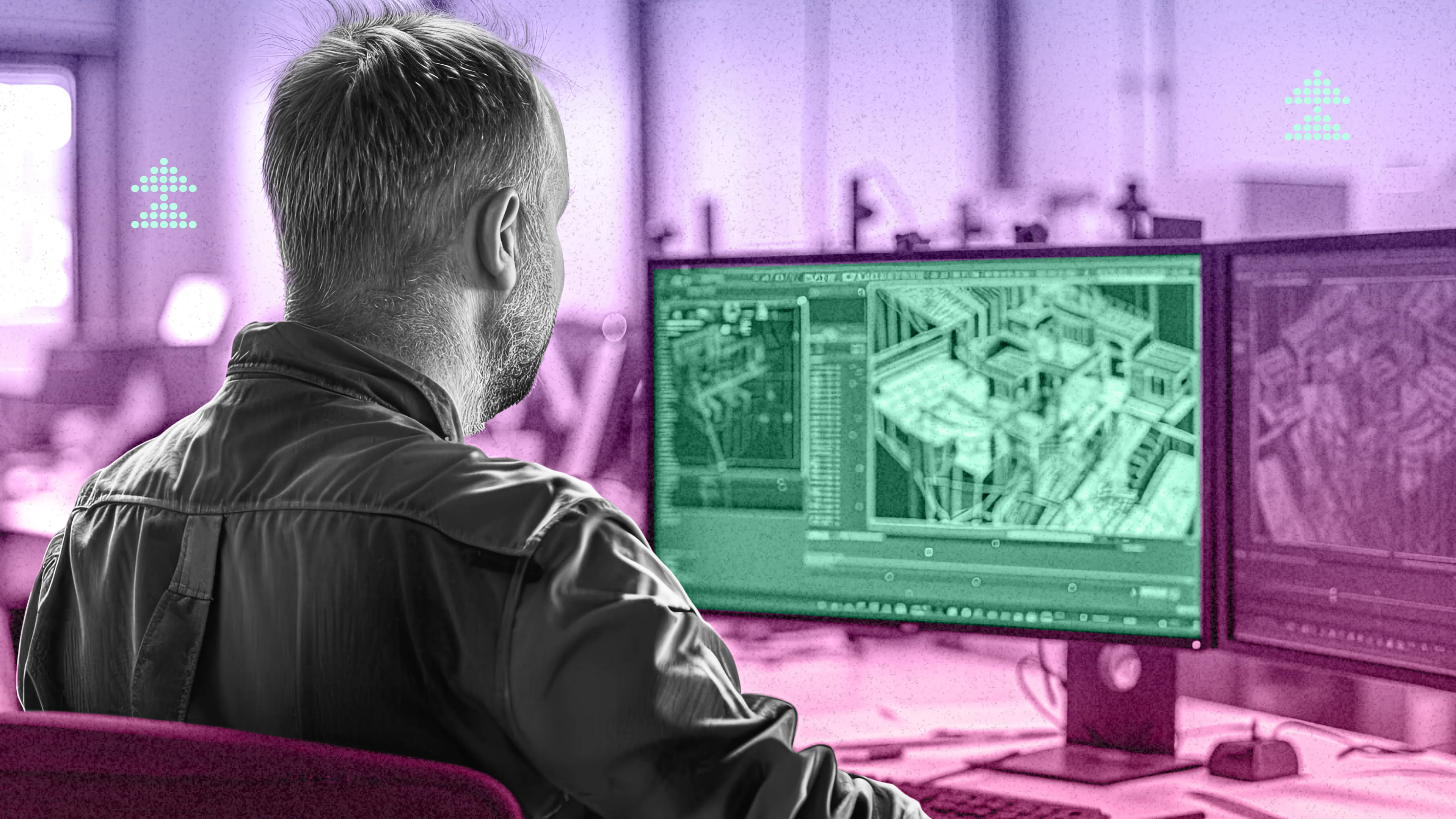
Bridging the Gap: How Simulated Designs Revolutionize Product Development
In the dynamic world of product design and engineering, simulated designs are transforming the way companies innovate and refine their products. By creating highly accurate digital prototypes, engineers can now test and validate concepts with unprecedented precision, dramatically reducing the time and cost associated with traditional physical prototyping.
These advanced simulations go beyond mere visual representations. They provide deep insights into product performance, stress tolerances, and potential failure points, allowing designers to make data-driven improvements before a single physical prototype is manufactured. This approach creates a powerful feedback loop of continuous improvement, where each simulation iteration brings the design closer to optimal performance.
The result is a more efficient, cost-effective, and innovative product development process. Companies can now explore complex design variations, predict real-world behaviors, and make strategic refinements—all within a virtual environment that mimics real-world conditions with remarkable accuracy.
By embracing simulation technologies, organizations are not just designing products; they're engineering excellence from the ground up.
Revolutionizing Manufacturing: The Cutting-Edge Frontier of Automated Design Innovation
In the rapidly evolving landscape of industrial engineering, a transformative revolution is quietly reshaping how manufacturers conceptualize, design, and produce complex systems. The convergence of advanced computational technologies, artificial intelligence, and sophisticated simulation techniques is unlocking unprecedented potential for innovation, efficiency, and precision in manufacturing processes.Breakthrough Technologies Redefining Product Development Paradigms
The Digital Twin Phenomenon: Bridging Virtual and Physical Realms
Modern manufacturing is experiencing a profound metamorphosis through digital twin technologies. These sophisticated virtual replicas transcend traditional modeling by creating hyper-realistic simulations that capture intricate mechanical interactions, material behaviors, and performance characteristics with extraordinary accuracy. Engineers can now predict product performance, stress tolerances, and potential failure points before a single physical prototype is constructed. By leveraging advanced machine learning algorithms and quantum computational capabilities, digital twin technologies enable manufacturers to conduct comprehensive virtual experiments. These simulations dramatically reduce development cycles, minimize material waste, and accelerate innovation by providing instantaneous insights into complex design challenges.Automated Assembly: Precision Engineering Meets Artificial Intelligence
The integration of artificial intelligence into automated assembly processes represents a quantum leap in manufacturing capabilities. Intelligent robotic systems now possess unprecedented adaptive learning capabilities, allowing them to optimize manufacturing workflows in real-time. These systems can dynamically adjust parameters, identify potential bottlenecks, and self-correct with minimal human intervention. Sophisticated machine vision technologies enable these automated systems to detect microscopic variations, ensuring consistent quality across production runs. By combining advanced sensor technologies with predictive analytics, manufacturers can achieve levels of precision and efficiency that were inconceivable just a decade ago.Computational Design Optimization: Reimagining Product Development
Computational design optimization has emerged as a game-changing approach to product development. Advanced algorithms can now generate thousands of design iterations, systematically exploring potential configurations that human designers might never conceive. These generative design techniques leverage artificial intelligence to create solutions that balance multiple complex constraints simultaneously. By analyzing historical performance data, material properties, and engineering requirements, these computational systems can produce designs that are simultaneously more efficient, lighter, and more structurally robust. The result is a new generation of products that push the boundaries of what's technically possible, achieving unprecedented levels of performance and sustainability.Sustainable Manufacturing: The Ecological Imperative
The convergence of automated design and simulation technologies is driving a profound ecological transformation in manufacturing. By enabling more precise material usage, reducing waste, and optimizing energy consumption, these advanced technologies are helping industries dramatically reduce their environmental footprint. Intelligent design systems can now model entire product lifecycles, considering not just initial manufacturing processes but also long-term sustainability implications. This holistic approach allows engineers to create products that are inherently more recyclable, energy-efficient, and aligned with emerging environmental standards.The Human-Machine Collaboration Paradigm
Contrary to fears of technological displacement, the future of manufacturing represents a sophisticated collaboration between human creativity and machine intelligence. Advanced design systems augment human capabilities, providing engineers with powerful tools to explore complex design spaces and make more informed decisions. This symbiotic relationship allows human designers to focus on high-level strategic thinking while automated systems handle intricate computational and analytical tasks. The result is a more dynamic, innovative, and responsive approach to product development that leverages the unique strengths of both human intuition and machine precision.RELATED NEWS
Manufacturing
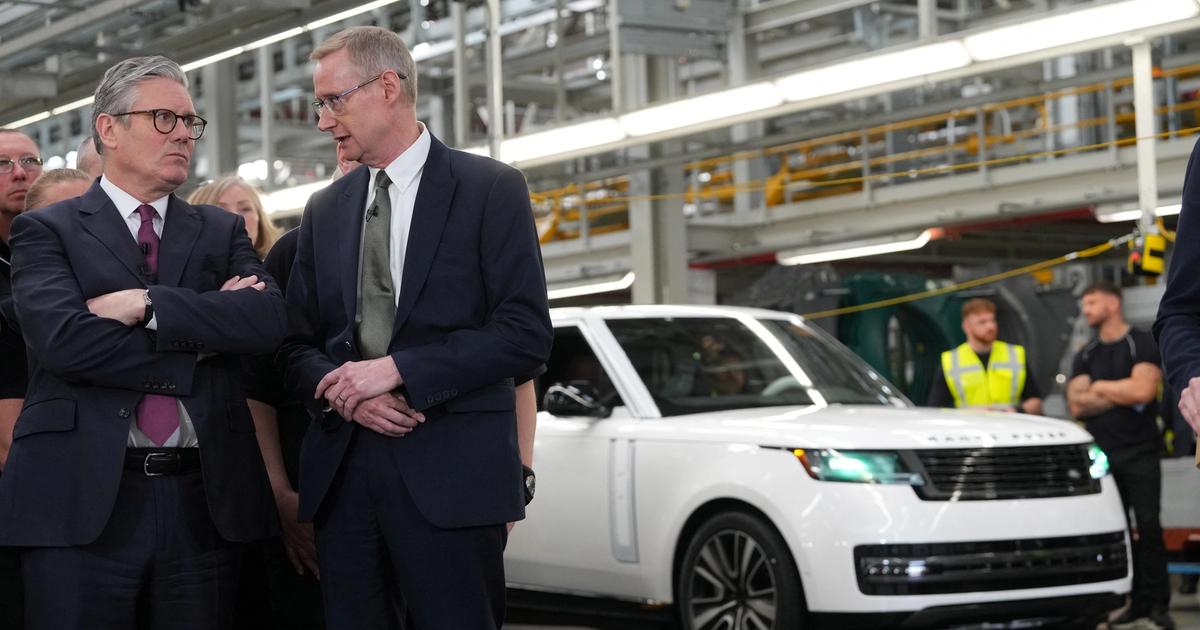
Manufacturing Meltdown: UK Industry Buckles Under Global Trade Tensions
2025-05-01 13:53:14
Manufacturing
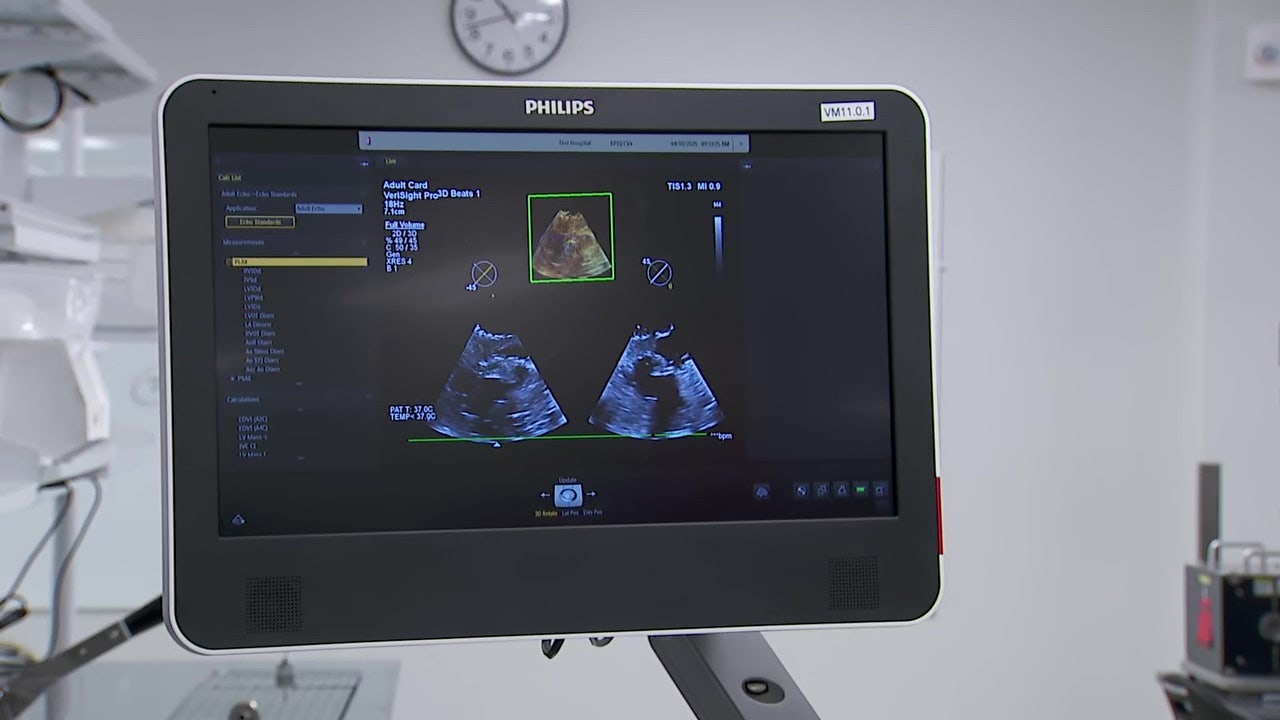
Manufacturing Renaissance: Walz Celebrates Philips' Minnesota Comeback
2025-04-10 17:08:02
Manufacturing
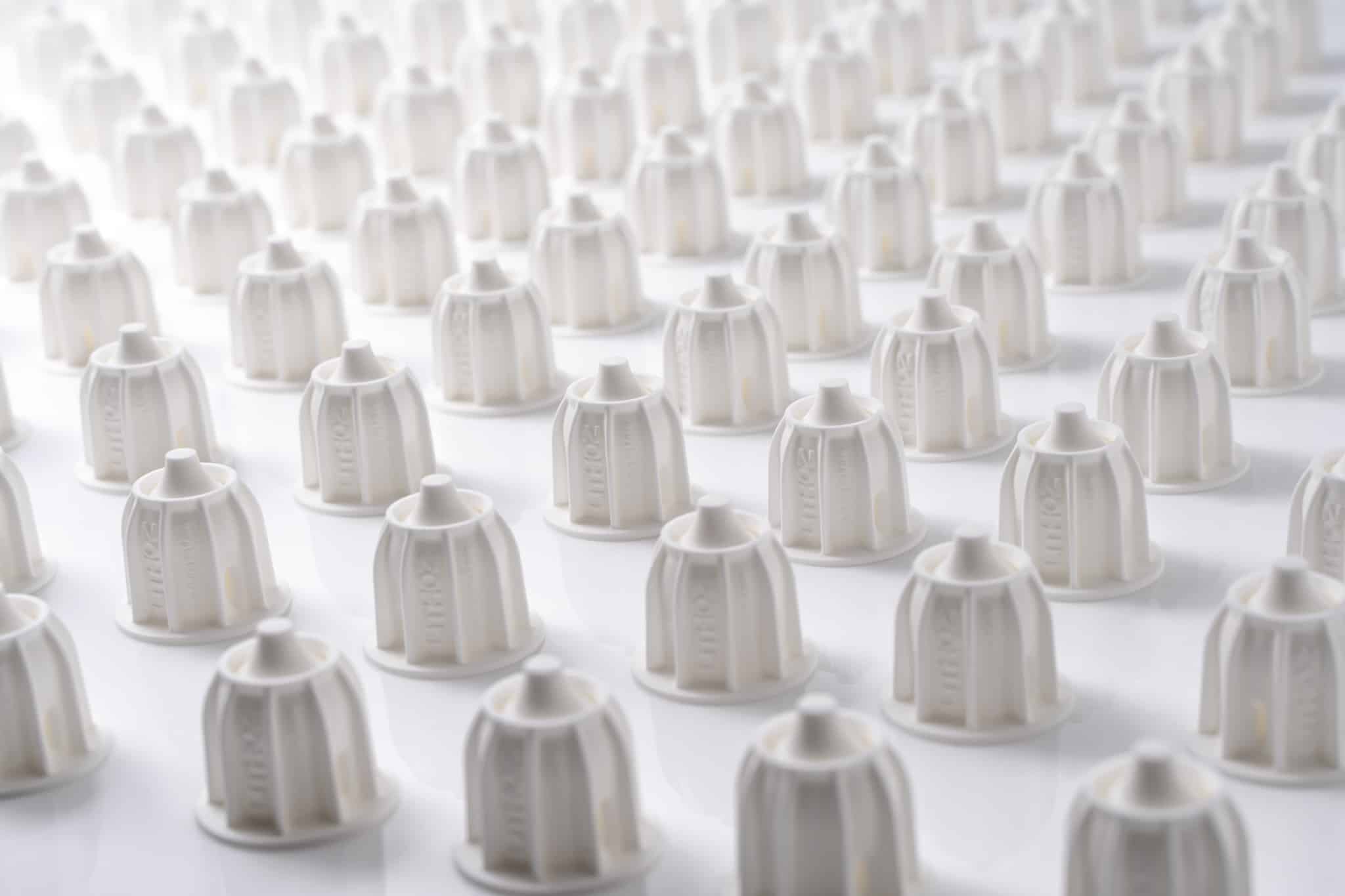
Revolutionizing Manufacturing: The Ceramic 3D Printing Pioneers Reshaping Industry Frontiers
2025-03-26 09:18:20