Titans of Steel: Inside the Massive Mill Shaft Revolution Transforming Heavy Industry
Manufacturing
2025-03-23 23:08:18Content
The Art of Crafting Colossal Mill Shafts: Engineering Marvels of Industrial Precision
Step into the fascinating world of heavy industrial manufacturing, where massive mill shafts are transformed from raw steel into extraordinary engineering masterpieces. These critical components represent the pinnacle of mechanical innovation, serving as the backbone of industrial machinery across the globe.
The journey begins with carefully selected high-grade steel, meticulously chosen for its exceptional strength and resilience. Expert metallurgists and skilled craftsmen collaborate to orchestrate a complex transformation process that pushes the boundaries of modern engineering.
Advanced Computer Numerical Control (CNC) technology takes center stage, guiding precision cutting and machining with microscopic accuracy. Massive forging presses apply tremendous heat and pressure, reshaping raw metal into robust, intricate shaft designs that can withstand extreme industrial conditions.
Heat treatment becomes a crucial phase, where sophisticated thermal processes enhance the steel's molecular structure, dramatically improving its durability and resistance to mechanical stress. Each shaft undergoes rigorous quality control, with multiple inspections ensuring it meets exacting international standards.
The result is nothing short of remarkable: mill shafts that represent the perfect fusion of human expertise and cutting-edge technological innovation. These engineering marvels power everything from massive mining equipment to complex industrial processing systems, silently driving the machinery that keeps our modern world moving.
From initial concept to final product, these extraordinary components embody the pinnacle of industrial craftsmanship—a testament to human ingenuity and technological advancement.
Forging Giants: The Intricate Art of Crafting Massive Industrial Mill Shafts
In the heart of modern industrial manufacturing, a remarkable process unfolds that transforms raw steel into engineering marvels. These colossal mill shafts represent more than mere mechanical components; they are the silent titans that power global industrial infrastructure, embodying human ingenuity and technological precision.Engineering Excellence: Where Strength Meets Innovation
The Genesis of Industrial Precision
The creation of massive mill shafts begins with an intricate dance of metallurgy and advanced engineering. Unlike conventional manufacturing processes, these extraordinary components demand an unprecedented level of expertise and technological sophistication. Metallurgists and engineers collaborate meticulously, selecting premium-grade steel alloys that can withstand extreme mechanical stress and environmental challenges. The initial stages involve comprehensive material selection, where engineers analyze molecular structures, tensile strengths, and potential performance characteristics. Each steel composition undergoes rigorous computational modeling to predict potential stress points, thermal expansion, and long-term durability. This preliminary analysis ensures that the final product will not merely meet but exceed industrial expectations.Transformative Forging Techniques
Modern forging represents a symphony of technological prowess and traditional craftsmanship. Massive hydraulic presses, capable of generating thousands of tons of pressure, reshape raw steel billets into preliminary shaft geometries. These machines apply controlled deformation, realigning metal grain structures to enhance inherent material strength. Temperature plays a critical role in this metamorphosis. Specialized furnaces heat steel to precise temperatures, typically between 900 and 1,250 degrees Celsius, allowing metallurgists to manipulate material properties. The controlled heating and subsequent controlled cooling create microstructural changes that significantly improve mechanical characteristics, introducing enhanced toughness and resistance to fatigue.Precision Machining: The Art of Microscopic Perfection
Once forged, these nascent shafts enter a realm of extraordinary precision. Computer Numerical Control (CNC) machines, equipped with diamond-tipped cutting tools, begin the meticulous process of dimensional refinement. These machines operate with tolerances measured in micrometers, ensuring geometric accuracy that defies human visual perception. Multi-axis machining centers rotate and manipulate shafts, removing microscopic layers of material to achieve perfect cylindrical symmetry. Laser measurement systems continuously monitor dimensional accuracy, providing real-time feedback that allows instantaneous adjustments. This level of precision ensures that each shaft will integrate seamlessly into complex industrial machinery.Thermal Treatment: Unlocking Material Potential
Heat treatment represents a transformative stage where material science reaches its zenith. Specialized thermal chambers subject shafts to carefully orchestrated temperature cycles, fundamentally altering their metallurgical structure. Processes like normalization, quenching, and tempering introduce specific material characteristics that enhance mechanical performance. Induction heating systems provide uniform thermal distribution, preventing structural inconsistencies. Advanced cooling techniques, including controlled atmospheric environments, ensure that material properties are optimized. The result is a component with exceptional hardness, improved wear resistance, and remarkable structural integrity.Quality Assurance: Beyond Conventional Inspection
The final frontier of mill shaft production involves comprehensive quality verification. Non-destructive testing methodologies like ultrasonic scanning, magnetic particle inspection, and advanced radiographic techniques scrutinize every microscopic detail. These sophisticated diagnostic tools can detect potential microscopic defects invisible to traditional visual inspection. Computerized tomography scanners provide three-dimensional internal views, revealing potential metallurgical anomalies. Each shaft undergoes multiple verification stages, with rejection rates often exceeding industry standards. This rigorous approach ensures that only components meeting extraordinary performance criteria proceed to industrial deployment.Global Impact and Future Horizons
These meticulously crafted mill shafts represent more than industrial components; they are embodiments of human technological achievement. From mining operations to renewable energy infrastructure, these precision-engineered marvels facilitate global industrial progress. As technological boundaries continue expanding, the art of creating these extraordinary components will undoubtedly evolve, pushing the frontiers of engineering excellence.RELATED NEWS
Manufacturing
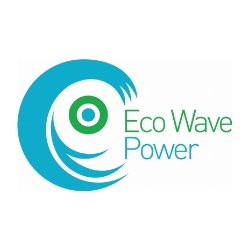
Riding the Green Wave: Eco Wave Power Breaks Ground on Revolutionary Los Angeles Maritime Energy Project
2025-04-23 12:00:00
Manufacturing
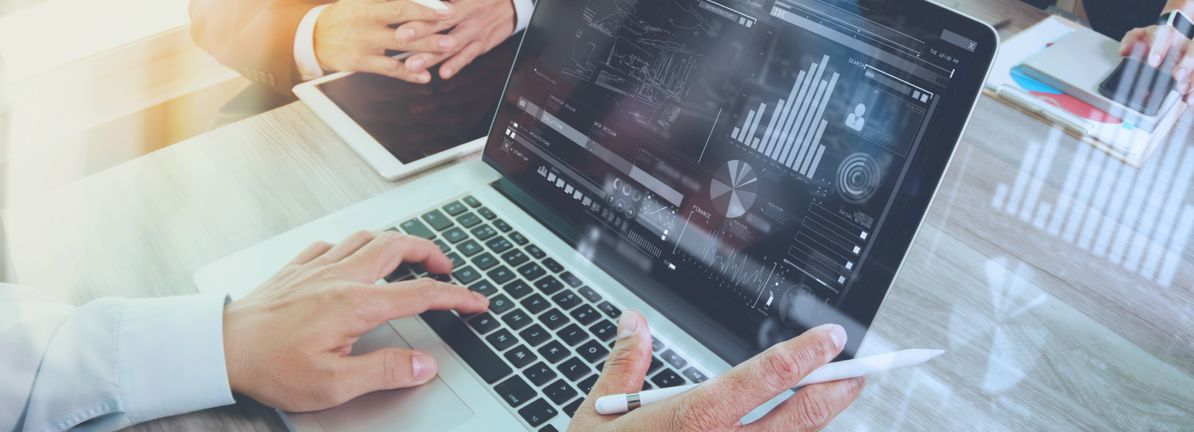
AI Revolution: Palantir Supercharges Manufacturing with Cutting-Edge Vatn Systems Partnership
2025-04-16 17:59:09
Manufacturing
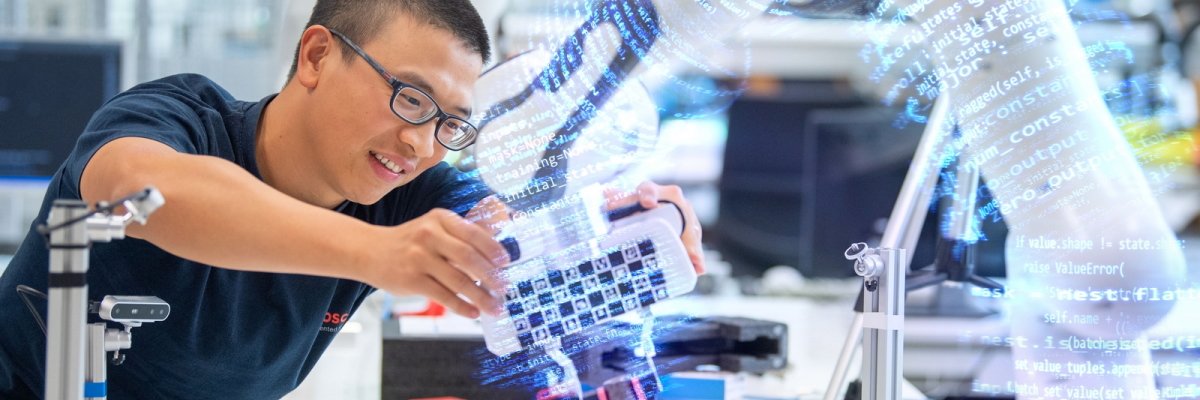
Beyond Automation: How Industry 5.0 is Reshaping the Future of Manufacturing
2025-02-26 05:45:00