3D Printing Revolution: How Next-Gen Tech is Transforming Manufacturing Certification
Manufacturing
2025-03-20 10:21:13Content
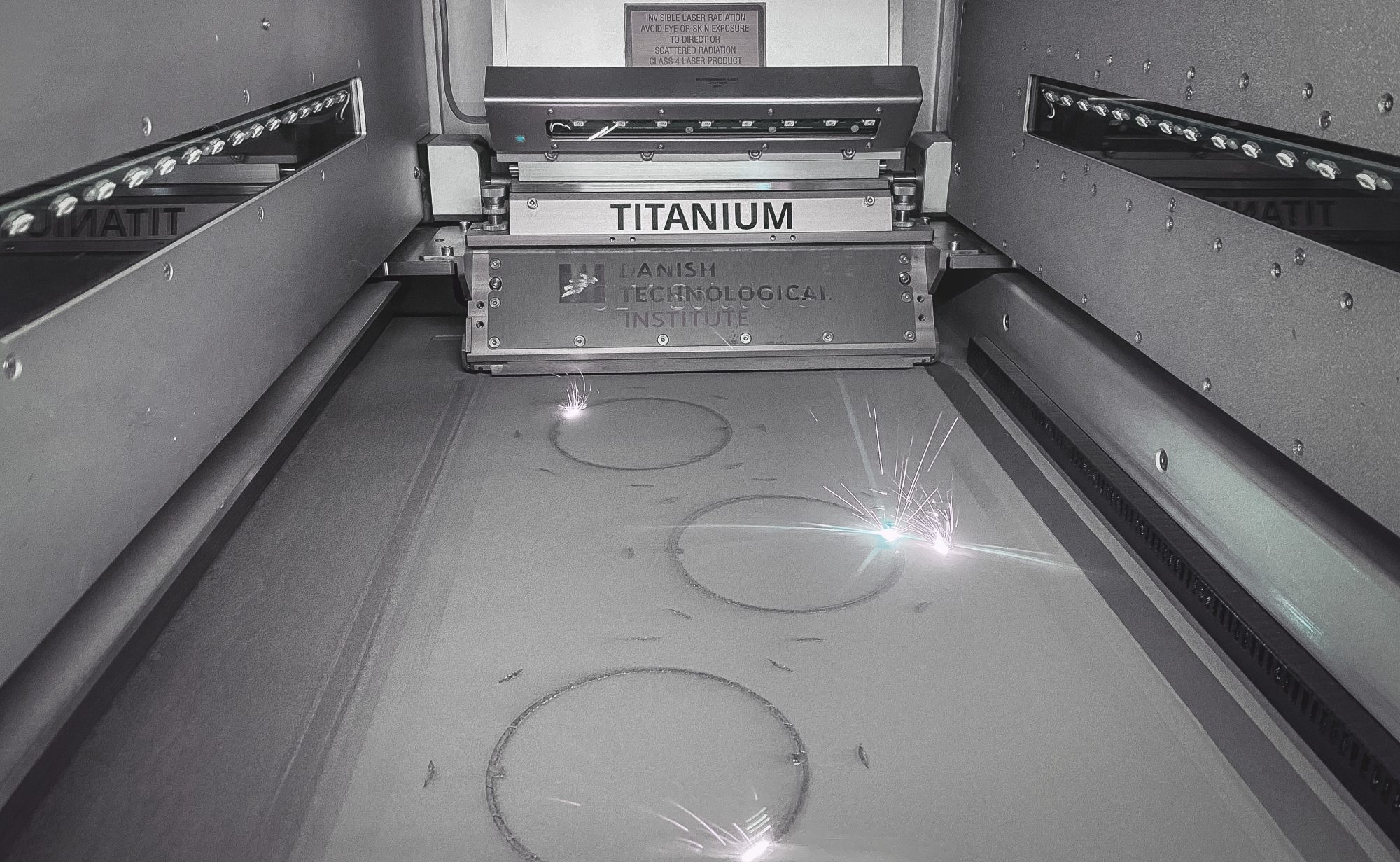
Pioneering the Future of Additive Manufacturing: DILAPRO's Revolutionary Approach
In the rapidly evolving world of advanced manufacturing, researchers are breaking new ground in additive manufacturing technologies. The DILAPRO project stands at the forefront of this innovation, offering a transformative approach to enhancing efficiency and streamlining certification processes.
At its core, DILAPRO represents a breakthrough in addressing critical challenges within additive manufacturing. The project focuses on developing sophisticated methodologies that dramatically improve production workflows and quality assurance mechanisms. By integrating cutting-edge data analysis and precision engineering techniques, DILAPRO enables manufacturers to achieve unprecedented levels of reliability and performance.
Key innovations include:
• Advanced process monitoring systems
• Intelligent data integration techniques
• Comprehensive certification protocols
• Real-time quality control mechanisms
The project's unique approach allows manufacturers to overcome traditional limitations in additive manufacturing, reducing production times and minimizing potential errors. By creating more robust and transparent manufacturing processes, DILAPRO is setting new industry standards for precision and efficiency.
Researchers involved in the project emphasize that DILAPRO is not just about technological advancement, but about reimagining the entire manufacturing ecosystem. The innovative framework promises to accelerate adoption of additive manufacturing across multiple industries, from aerospace and automotive to medical device production.
As manufacturing continues to evolve, DILAPRO represents a critical step towards more intelligent, responsive, and reliable production technologies.
Revolutionizing Manufacturing: The DILAPRO Breakthrough in Additive Innovation
In the rapidly evolving landscape of advanced manufacturing, technological breakthroughs are reshaping how industries approach production, design, and efficiency. The emergence of cutting-edge additive manufacturing techniques represents a pivotal moment in industrial innovation, promising to transform traditional manufacturing paradigms and unlock unprecedented potential for precision, customization, and performance.Transforming Production: Where Technology Meets Unprecedented Precision
The Technological Frontier of Additive Manufacturing
Modern manufacturing stands at a critical intersection of technological innovation and practical application. Additive manufacturing, often referred to as 3D printing, has emerged as a transformative technology that challenges conventional production methodologies. Unlike traditional subtractive manufacturing processes that remove material to create components, additive manufacturing builds objects layer by layer, offering unprecedented design flexibility and material efficiency. The DILAPRO system represents a quantum leap in this technological domain, integrating advanced computational algorithms with sophisticated material deposition techniques. By leveraging precision engineering and intelligent design protocols, the system enables manufacturers to create complex geometries that were previously impossible or prohibitively expensive to produce.Precision Engineering and Certification Challenges
Certification in advanced manufacturing remains a complex and rigorous process, particularly in industries with stringent quality requirements such as aerospace, medical devices, and high-performance engineering. The DILAPRO approach addresses these challenges through a multifaceted strategy that combines real-time monitoring, advanced material characterization, and predictive analytics. By implementing sophisticated sensor networks and machine learning algorithms, the system can continuously track and validate manufacturing parameters. This approach ensures that each produced component meets exacting standards, reducing variability and enhancing overall product reliability. The integration of comprehensive data collection and analysis mechanisms allows for unprecedented transparency and quality control throughout the manufacturing process.Material Innovation and Performance Optimization
The true potential of additive manufacturing lies not just in its production methodology but in its ability to reimagine material properties and performance characteristics. DILAPRO's technological framework enables researchers and engineers to experiment with novel material compositions, exploring hybrid structures and advanced alloys that push the boundaries of traditional manufacturing limitations. Through precise layer-by-layer deposition and sophisticated thermal management techniques, the system can create components with tailored mechanical properties, enhanced structural integrity, and optimized weight-to-strength ratios. This capability is particularly crucial in industries like aerospace and automotive, where material efficiency can translate directly into performance improvements and significant energy savings.Economic and Sustainability Implications
Beyond technical capabilities, the DILAPRO approach carries profound economic and environmental implications. By minimizing material waste, reducing energy consumption, and enabling more localized production strategies, the technology represents a significant step towards more sustainable manufacturing practices. The ability to produce complex components with minimal material input challenges traditional supply chain models, potentially reducing transportation costs, inventory requirements, and overall carbon footprint. Moreover, the technology democratizes manufacturing capabilities, allowing smaller enterprises to compete with larger industrial players through access to advanced production technologies.Future Perspectives and Research Directions
As additive manufacturing continues to evolve, technologies like DILAPRO are not merely incremental improvements but fundamental reimaginings of production methodologies. Ongoing research focuses on expanding material compatibility, improving computational modeling techniques, and developing more sophisticated certification protocols. The convergence of artificial intelligence, advanced materials science, and precision engineering promises to unlock new frontiers in manufacturing, with potential applications ranging from personalized medical implants to complex aerospace components and beyond. The DILAPRO system stands as a testament to human ingenuity and technological potential, bridging theoretical possibilities with practical industrial applications.RELATED NEWS
Manufacturing
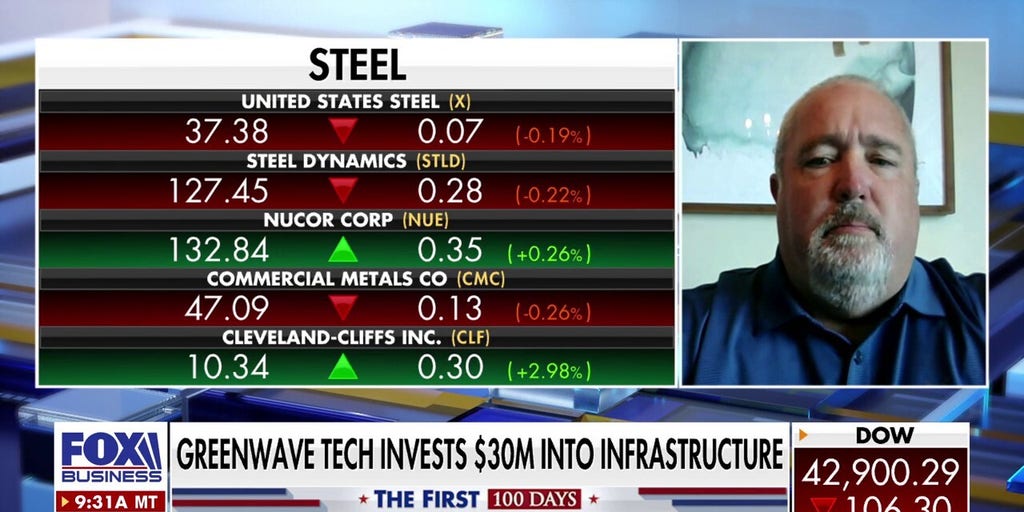
Steel's Comeback: How Trump's Tariffs Are Leveling the Industrial Battlefield
2025-03-06 17:36:50
Manufacturing
Grid Revolution: Switched Source Pumps $5M into Cutting-Edge Manufacturing Hub
2025-03-20 10:00:00
Manufacturing
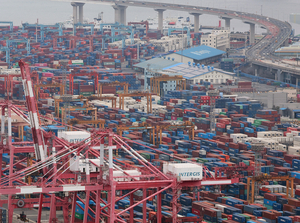
Industrial Shock: South Korean Manufacturing Suffers Steepest Decline in Over a Year and a Half
2025-03-09 02:39:21