Robots Meet Luxury: Mercedes-Benz Revolutionizes Production with AI and Humanoid Workers
Manufacturing
2025-03-19 15:41:25Content
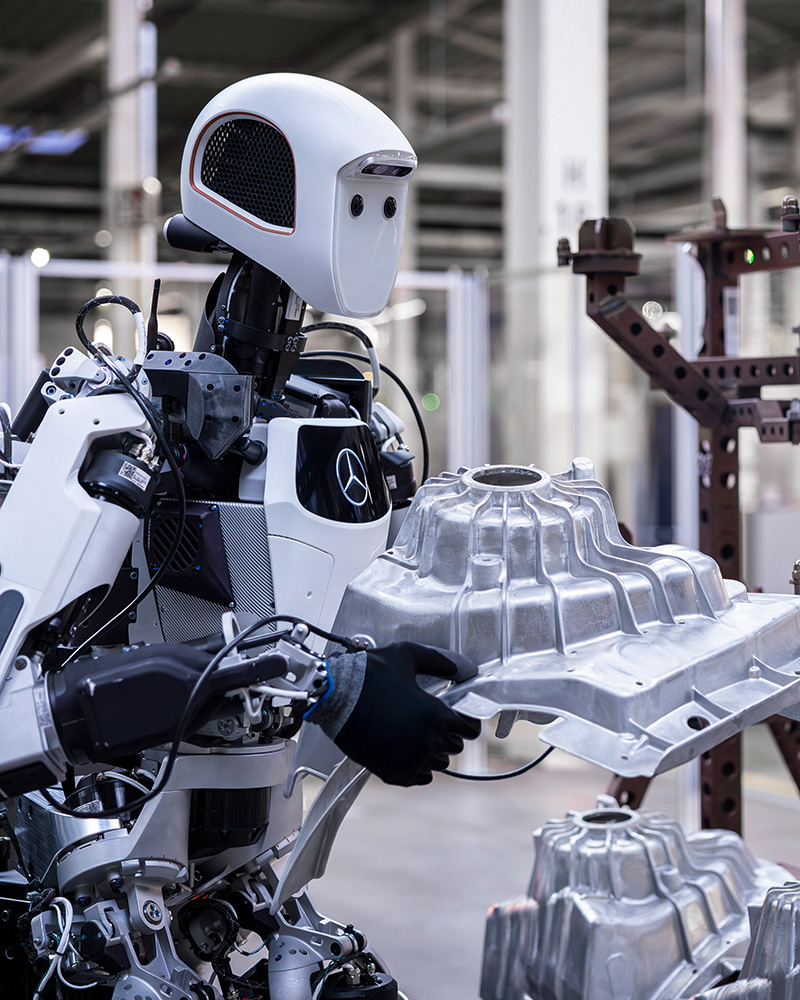
Mercedes-Benz is revolutionizing automotive manufacturing by seamlessly blending cutting-edge technology with human expertise at its innovative Digital Factory Campus in Berlin-Marienfelde, Germany. The company has taken a bold step forward by introducing Apollo, a groundbreaking humanoid robot that represents the pinnacle of commercial robotic technology.
This strategic integration of artificial intelligence and advanced robotics marks a significant milestone in the company's commitment to enhancing production efficiency and sustainability. Apollo is not just another industrial machine, but a sophisticated technological marvel designed to work alongside human employees, streamlining complex manufacturing processes and pushing the boundaries of what's possible in modern automotive production.
By deploying these state-of-the-art humanoid robots, Mercedes-Benz is demonstrating its forward-thinking approach to manufacturing, showcasing how intelligent automation can transform traditional production methods. The Digital Factory Campus serves as a testament to the company's vision of creating a more adaptive, precise, and innovative automotive production ecosystem.
As the automotive industry continues to evolve, Mercedes-Benz is positioning itself at the forefront of technological innovation, proving that the future of manufacturing lies in the harmonious collaboration between human creativity and robotic precision.
Robotic Revolution: Mercedes-Benz Transforms Manufacturing with Cutting-Edge AI and Humanoid Technology
In the rapidly evolving landscape of automotive manufacturing, Mercedes-Benz is pioneering a groundbreaking transformation that promises to redefine the future of industrial production. By integrating advanced artificial intelligence and state-of-the-art humanoid robotics, the company is setting new benchmarks for technological innovation and operational efficiency in the automotive sector.Where Human Ingenuity Meets Robotic Precision: The Next Frontier of Manufacturing
The Digital Factory Campus: A Technological Sanctuary of Innovation
The Berlin-Marienfelde facility represents more than just a manufacturing site; it's a visionary ecosystem where technological boundaries are continuously pushed and redefined. Mercedes-Benz has strategically positioned this campus as a crucible of innovation, where cutting-edge robotics and artificial intelligence converge to create unprecedented manufacturing capabilities. The integration of humanoid robots like Apollo signals a profound shift in how automotive production will be conceptualized and executed in the coming decades. The Digital Factory Campus embodies a holistic approach to technological integration, where each robotic system is meticulously designed to complement human capabilities rather than replace them. By creating a symbiotic environment between human workers and advanced robotic systems, Mercedes-Benz is demonstrating a nuanced understanding of technological evolution that goes beyond mere automation.Apollo: Redefining the Boundaries of Robotic Capabilities
Apollo represents a quantum leap in humanoid robotics, transcending traditional industrial automation paradigms. Unlike conventional robotic systems that are typically rigid and single-purpose, Apollo demonstrates remarkable adaptability and sophisticated cognitive processing capabilities. Its design incorporates advanced machine learning algorithms that enable real-time decision-making and complex task navigation. The robot's architectural sophistication allows it to perform intricate manufacturing tasks with unprecedented precision. From delicate component assembly to complex quality control processes, Apollo showcases a level of dexterity and intelligence that challenges existing perceptions of robotic potential. Mercedes-Benz has essentially created a technological marvel that bridges the gap between human intuition and machine efficiency.Artificial Intelligence: The Intelligent Nervous System of Modern Manufacturing
Artificial intelligence serves as the cerebral infrastructure driving Mercedes-Benz's revolutionary manufacturing approach. By implementing sophisticated AI algorithms, the company can optimize production workflows, predict maintenance requirements, and dynamically adjust manufacturing processes in real-time. This intelligent system goes beyond traditional predictive maintenance, creating a self-evolving manufacturing environment that continuously learns and improves. The AI's capabilities extend far beyond operational optimization. It provides comprehensive data analytics that offer unprecedented insights into production efficiency, resource allocation, and potential improvement areas. By transforming raw operational data into actionable intelligence, Mercedes-Benz is establishing a new standard for data-driven manufacturing strategies.Sustainability and Efficiency: The Dual Pillars of Technological Transformation
Mercedes-Benz's technological integration is fundamentally driven by a commitment to sustainability and operational efficiency. The humanoid robots and AI systems consume significantly less energy compared to traditional manufacturing equipment while delivering superior performance. This approach not only reduces carbon footprint but also demonstrates a forward-thinking commitment to environmental responsibility. The efficiency gains are equally impressive. By minimizing human error, optimizing workflow, and enabling 24/7 production capabilities, the robotic systems dramatically enhance overall manufacturing productivity. Each technological enhancement represents a calculated step towards creating a more intelligent, responsive, and sustainable manufacturing ecosystem.The Human-Machine Collaboration Paradigm
Contrary to dystopian narratives about robots replacing humans, Mercedes-Benz's approach emphasizes collaborative potential. The humanoid robots are designed to work alongside human employees, augmenting their capabilities and handling tasks that are physically demanding or precision-critical. This collaborative model ensures that human creativity and intuition remain central to the manufacturing process while leveraging robotic precision and endurance. Training programs and ergonomic workplace designs further underscore the company's commitment to creating a harmonious human-machine work environment. Employees are not just observers but active participants in this technological transformation, receiving specialized training to effectively interact with and manage advanced robotic systems.RELATED NEWS
Manufacturing
Job Market Shock: Oregon's Employment Landscape Crumbles as Manufacturing Sector Takes Brutal Hit
2025-03-11 19:59:28
Manufacturing

Manufacturing's Comeback: 3 Game-Changing Trends Reshaping American Industry
2025-04-10 19:18:00
Manufacturing
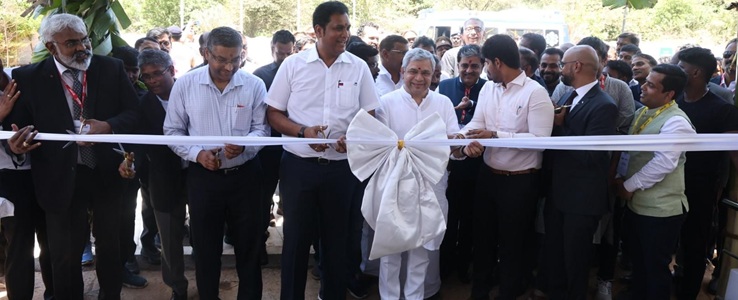
Manufacturing Momentum: Zetwerk Expands Footprint with Tamil Nadu Plant, Eyes Public Listing
2025-03-18 05:00:00