From Classroom to Factory Floor: How Pittsburgh's Bold Training Program Is Reshaping Manufacturing Careers
Manufacturing
2025-03-19 11:00:00Content
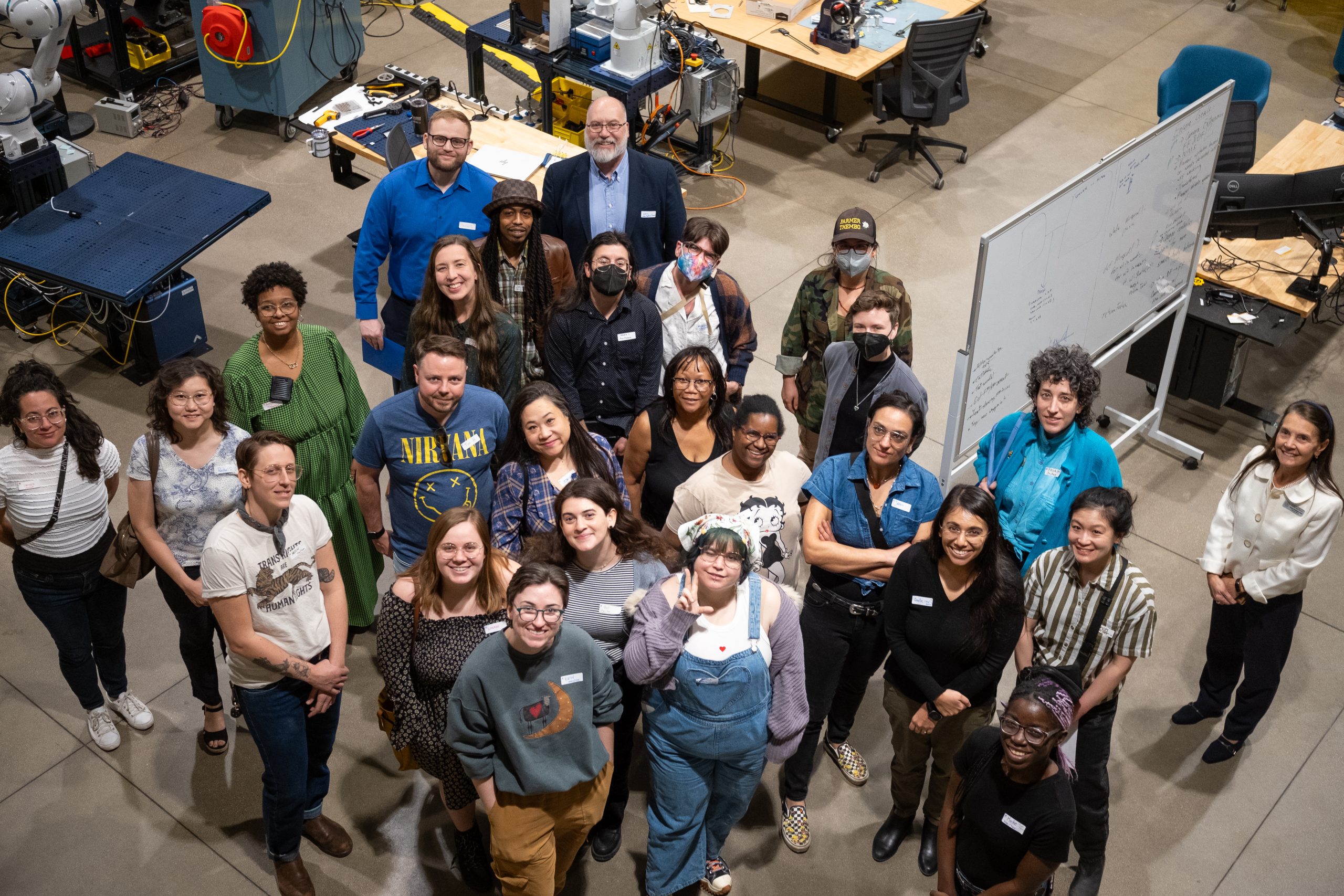
In the heart of Pittsburgh's industrial landscape, Erin Gatz, founder of Prototype PGH, recognized a critical gap in the local workforce. Her vision was clear: create meaningful pathways for Pittsburgh's existing community members to access promising manufacturing careers, rather than relying on outside talent.
Gatz understood that true economic empowerment begins with providing opportunities to local residents. By developing an innovative on-ramp program, she aimed to bridge the skills gap and transform the manufacturing sector from within, ensuring that Pittsburgh's own people could benefit from the city's industrial renaissance.
Her initiative represents more than just job training—it's about building community resilience, supporting local talent, and creating sustainable career opportunities for those who call Pittsburgh home. Through Prototype PGH, Gatz is rewriting the narrative of workforce development, one local worker at a time.
Bridging the Skills Gap: How Pittsburgh's Manufacturing Ecosystem is Transforming Local Workforce Development
In the heart of Pittsburgh's industrial landscape, a quiet revolution is brewing—one that challenges traditional workforce recruitment and champions local talent. As manufacturing sectors continue to evolve, innovative approaches are emerging to reconnect communities with meaningful career opportunities, transforming economic narratives and empowering individuals through strategic skill development.Revolutionizing Manufacturing Pathways: Local Talent, Global Potential
The Manufacturing Talent Paradox
Pittsburgh's industrial ecosystem has long grappled with a complex challenge: attracting skilled workers while simultaneously nurturing homegrown talent. Traditional recruitment strategies often prioritized external candidates, inadvertently overlooking the rich potential residing within local communities. This approach created a disconnection between available jobs and resident workforce capabilities, perpetuating cycles of economic marginalization. The manufacturing sector's transformation demands more than conventional hiring practices. It requires a holistic reimagining of workforce development, where local individuals are viewed not as passive recipients of opportunity, but as active architects of their professional futures. By creating intentional pathways that bridge skills gaps, organizations can unlock unprecedented potential within existing community networks.Prototype PGH: A Visionary Approach to Workforce Integration
Erin Gatz's pioneering initiative represents a paradigm shift in workforce development strategies. Prototype PGH emerges as a beacon of innovation, deliberately designing programs that transform manufacturing job access for local residents. Unlike traditional models that rely on external recruitment, this approach centers community members as primary stakeholders in their economic advancement. The organization's methodology goes beyond simple job placement, focusing instead on comprehensive skill development, personalized training, and creating sustainable career trajectories. By understanding the unique challenges faced by local workers, Prototype PGH develops targeted interventions that address systemic barriers to employment, ultimately reshaping the region's industrial landscape.Deconstructing Barriers, Constructing Opportunities
Manufacturing job accessibility involves dismantling complex socioeconomic barriers. These obstacles extend far beyond basic skill requirements, encompassing psychological, educational, and structural challenges that have historically marginalized certain community segments. Prototype PGH's approach recognizes these multifaceted dynamics, implementing holistic support mechanisms that address individual and collective needs. Strategic partnerships with local educational institutions, industry leaders, and community organizations form the backbone of this transformative model. By creating integrated ecosystems of support, the initiative ensures that workforce development is not a linear process, but a dynamic, responsive network that adapts to evolving industrial demands and individual aspirations.Technology, Training, and Transformation
Modern manufacturing demands continuous learning and technological adaptability. Prototype PGH's programs are meticulously designed to equip participants with cutting-edge skills that transcend traditional vocational training. Advanced technologies like robotics, precision engineering, and digital manufacturing become accessible through carefully crafted curriculum and hands-on learning experiences. The initiative's commitment to technological literacy ensures that local workers are not just employed, but are positioned at the forefront of industrial innovation. By demystifying complex technological landscapes and providing practical, industry-aligned training, Prototype PGH transforms potential into tangible career progression.Economic Empowerment Through Strategic Intervention
Beyond individual skill development, Prototype PGH's model represents a broader strategy of economic revitalization. By prioritizing local talent, the initiative contributes to community wealth generation, reduces unemployment, and creates multiplier effects that extend beyond immediate job placements. Each participant's journey becomes a testament to the power of targeted workforce development—demonstrating how strategic interventions can reshape individual trajectories and collective economic potential. The ripple effects of such approaches extend far beyond immediate employment, fostering long-term community resilience and industrial competitiveness.RELATED NEWS
Manufacturing
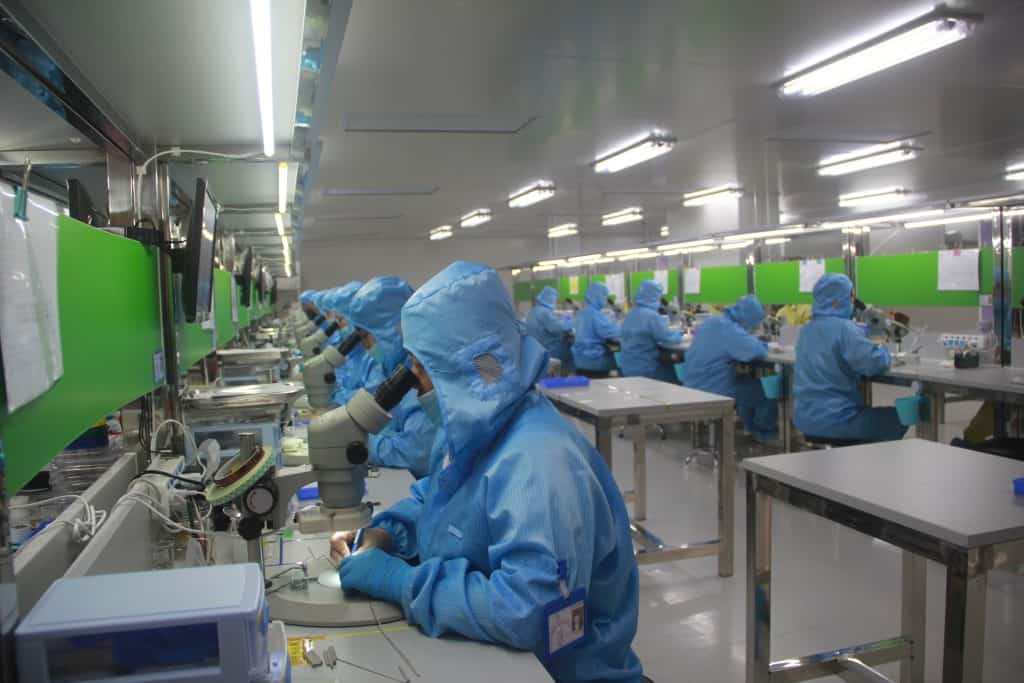
Breaking: CARBOGEN AMCIS Secures Game-Changing Manufacturing License to Expand China Services
2025-04-23 13:10:51
Manufacturing
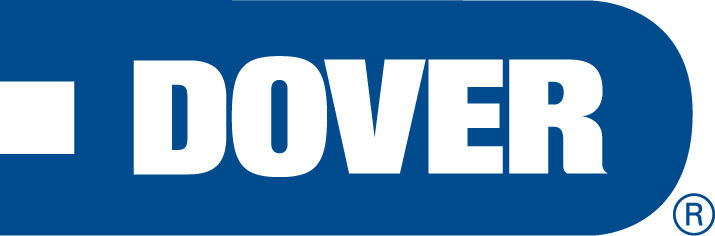
Precision Meets Innovation: Midland's Digital Breakthrough Transforms Railcar Measurement
2025-04-15 20:15:00
Manufacturing
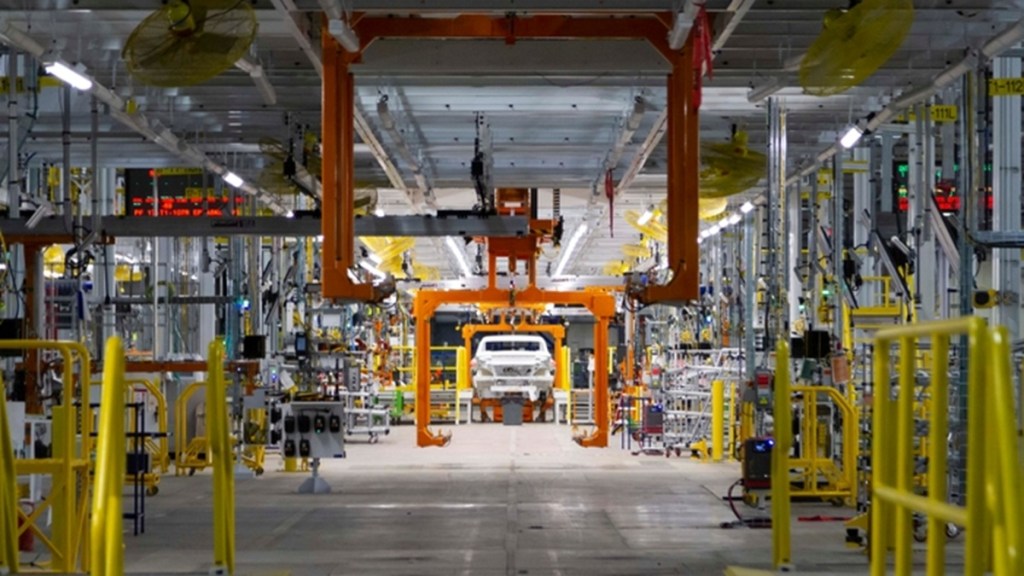
AI Powerhouse Fusion: GM and Nvidia Revolutionize Autonomous Driving Technology
2025-03-18 18:23:00