Workforce Revolution: 8 Game-Changing HR Strategies Transforming Manufacturing in 2024
Manufacturing
2025-03-18 14:48:00Content
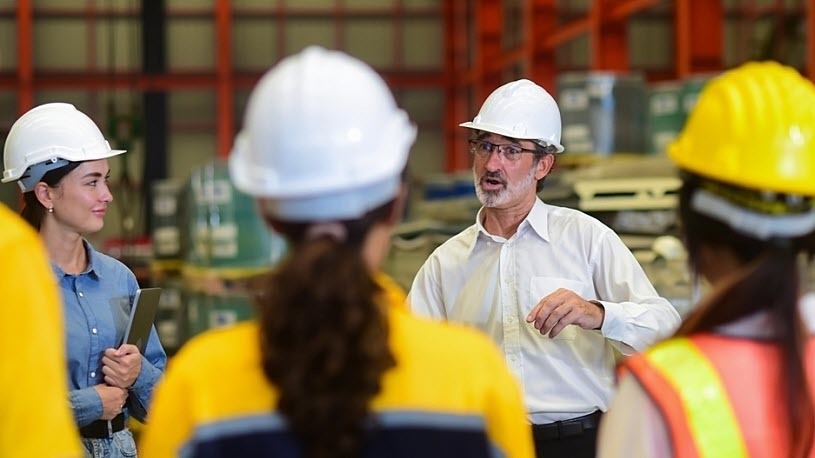
Manufacturing's Workforce Revolution: 8 HR and Talent Trends Shaping 2025
The manufacturing landscape is undergoing a dramatic transformation, with human resources and talent management at the forefront of this exciting evolution. As we approach 2025, industry leaders are navigating a complex ecosystem of workforce challenges and opportunities that will redefine how manufacturing organizations attract, develop, and retain top talent.
Key Trends Driving Workforce Innovation
- Digital Skills Integration: Manufacturers are increasingly prioritizing digital literacy, seeking professionals who can seamlessly blend traditional manufacturing expertise with cutting-edge technological skills.
- Adaptive Workforce Strategies: Flexible work arrangements and hybrid employment models are becoming the new standard, allowing companies to tap into global talent pools and enhance workforce resilience.
- Upskilling and Continuous Learning: Organizations are investing heavily in comprehensive training programs that enable employees to stay ahead of technological advancements and industry disruptions.
- Diversity and Inclusion Initiatives: Progressive manufacturers are implementing robust strategies to create more inclusive workplaces that attract diverse talent and foster innovation.
- Advanced Compliance Frameworks: Evolving regulatory landscapes are pushing companies to develop more sophisticated compliance and risk management approaches.
- AI-Powered Recruitment: Artificial intelligence is revolutionizing talent acquisition, enabling more precise candidate matching and predictive hiring strategies.
- Mental Health and Well-being: Comprehensive wellness programs are becoming critical in attracting and retaining top talent in a competitive job market.
- Sustainable Workforce Planning: Companies are aligning workforce strategies with broader environmental and social responsibility goals.
As manufacturing continues to evolve, organizations that embrace these trends will be best positioned to build agile, innovative, and resilient workforces capable of thriving in an increasingly complex global environment.
Revolutionizing Manufacturing: The Future of Workforce Dynamics in 2025
In the rapidly evolving landscape of industrial innovation, manufacturing stands at a critical crossroads. The traditional paradigms of workforce management are being dismantled and reconstructed, driven by technological advancements, changing global economic conditions, and unprecedented shifts in talent acquisition and retention strategies.Transforming Workforce Strategies: Where Technology Meets Human Potential
Digital Transformation and Workforce Adaptation
The manufacturing sector is experiencing a seismic shift in technological integration that fundamentally reimagines human capital. Artificial intelligence, machine learning, and advanced robotics are no longer futuristic concepts but immediate realities reshaping workforce dynamics. Companies must now develop comprehensive strategies that seamlessly blend human expertise with technological capabilities. Organizations are discovering that successful digital transformation isn't about replacing human workers, but empowering them with sophisticated tools and continuous learning opportunities. This requires creating adaptive learning environments where employees can rapidly upskill and reskill, ensuring they remain competitive in an increasingly automated landscape.Talent Acquisition in a Competitive Ecosystem
Recruiting top-tier talent has become an intricate dance of understanding emerging skill sets and anticipating future technological requirements. Manufacturing organizations are moving beyond traditional recruitment models, embracing data-driven approaches that leverage predictive analytics and comprehensive talent mapping. The most successful companies are developing holistic talent strategies that consider not just technical skills, but emotional intelligence, adaptability, and collaborative potential. This means creating workplace cultures that attract innovative thinkers who can navigate complex technological ecosystems while maintaining human-centric problem-solving approaches.Compliance and Regulatory Navigations
Regulatory landscapes are becoming increasingly complex, demanding manufacturers develop robust compliance frameworks that protect both organizational interests and employee rights. This involves creating sophisticated governance models that anticipate potential legal challenges while maintaining flexibility. Advanced compliance strategies now integrate technological solutions like AI-powered monitoring systems and real-time regulatory tracking. These tools enable organizations to proactively manage potential risks, ensuring workplace safety, ethical practices, and alignment with evolving global standards.Remote Work and Hybrid Manufacturing Models
The traditional manufacturing workplace is undergoing radical transformation. While certain roles remain inherently physical, technological innovations are creating unprecedented opportunities for remote and hybrid work models. This requires reimagining collaboration, communication, and productivity frameworks. Organizations must invest in sophisticated digital infrastructure that enables seamless communication between on-site and remote workers. This involves developing advanced collaboration platforms, implementing robust cybersecurity measures, and creating inclusive cultural practices that transcend physical workplace boundaries.Sustainable Workforce Development
Sustainability is no longer just an environmental concept but a comprehensive approach to workforce development. Manufacturing leaders are recognizing that long-term success depends on creating regenerative workforce ecosystems that prioritize employee well-being, continuous learning, and holistic professional growth. This means developing comprehensive professional development programs, mental health support systems, and career progression frameworks that view employees as long-term strategic assets rather than replaceable resources. Companies must create environments that nurture individual potential while aligning with broader organizational objectives.Technological Skills and Human Creativity
The future of manufacturing lies in the delicate balance between technological proficiency and human creativity. While automation continues to advance, the most valuable employees will be those who can leverage technology creatively, solve complex problems, and bring innovative perspectives to technological challenges. Organizations must create learning environments that encourage experimentation, critical thinking, and interdisciplinary skill development. This involves breaking down traditional departmental silos and fostering collaborative, cross-functional learning experiences.Global Talent Ecosystem
Manufacturing is becoming increasingly globalized, requiring organizations to develop sophisticated strategies for accessing and managing international talent pools. This involves understanding diverse cultural contexts, developing inclusive recruitment practices, and creating flexible work arrangements that transcend geographical boundaries. Successful companies will be those that can effectively navigate complex international talent markets, leveraging technological platforms to create seamless, borderless workforce experiences.Ethical Technology Integration
As technological capabilities expand, manufacturers must prioritize ethical considerations in workforce development. This means developing comprehensive frameworks that ensure technological implementation respects human dignity, promotes fairness, and mitigates potential negative societal impacts. Organizations must proactively address potential ethical challenges, creating transparent decision-making processes that balance technological efficiency with human-centric values.RELATED NEWS
Manufacturing
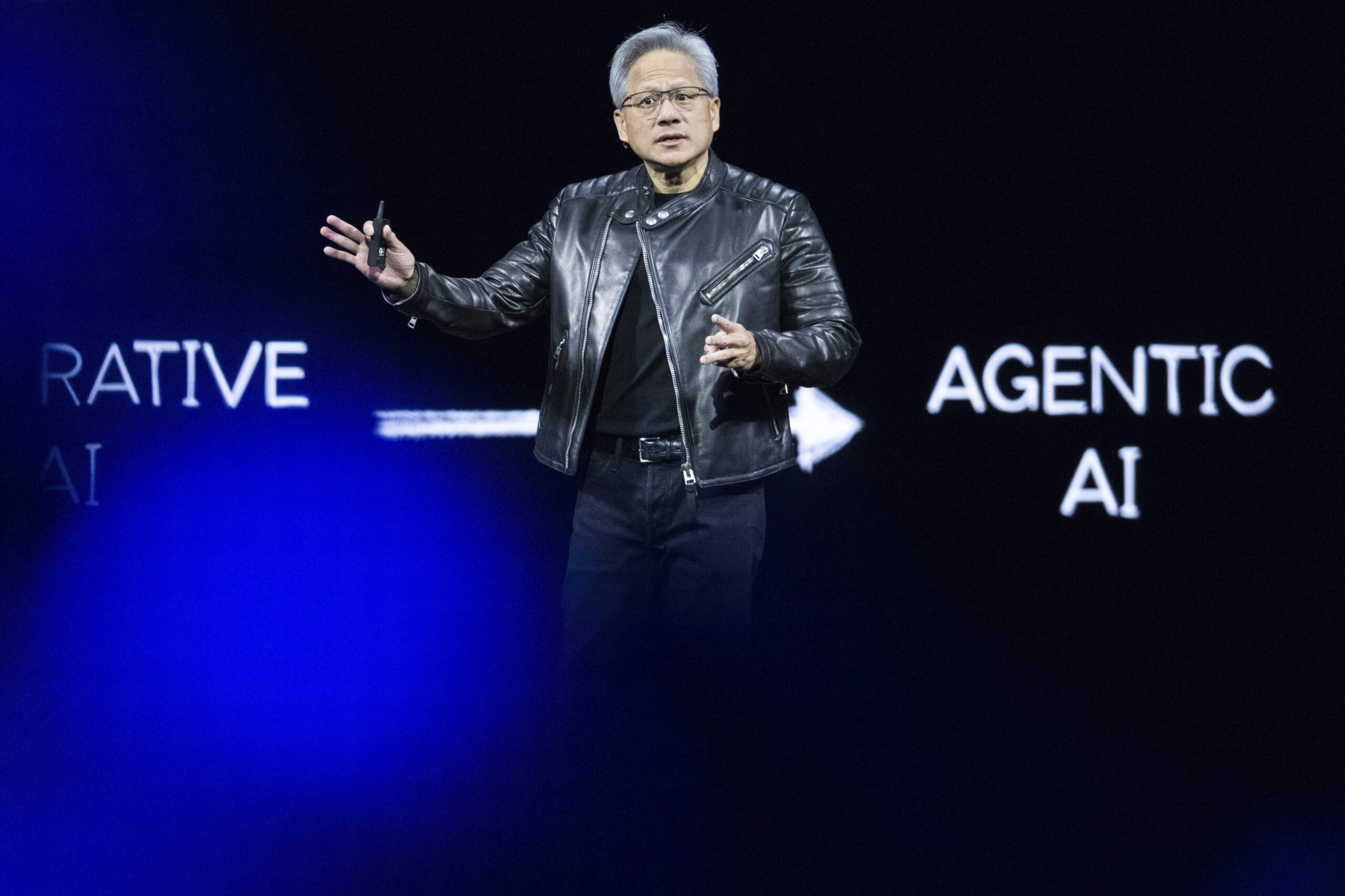
Chip Revolution: Nvidia Brings AI Silicon Manufacturing Home to American Soil
2025-04-14 16:58:00
Manufacturing
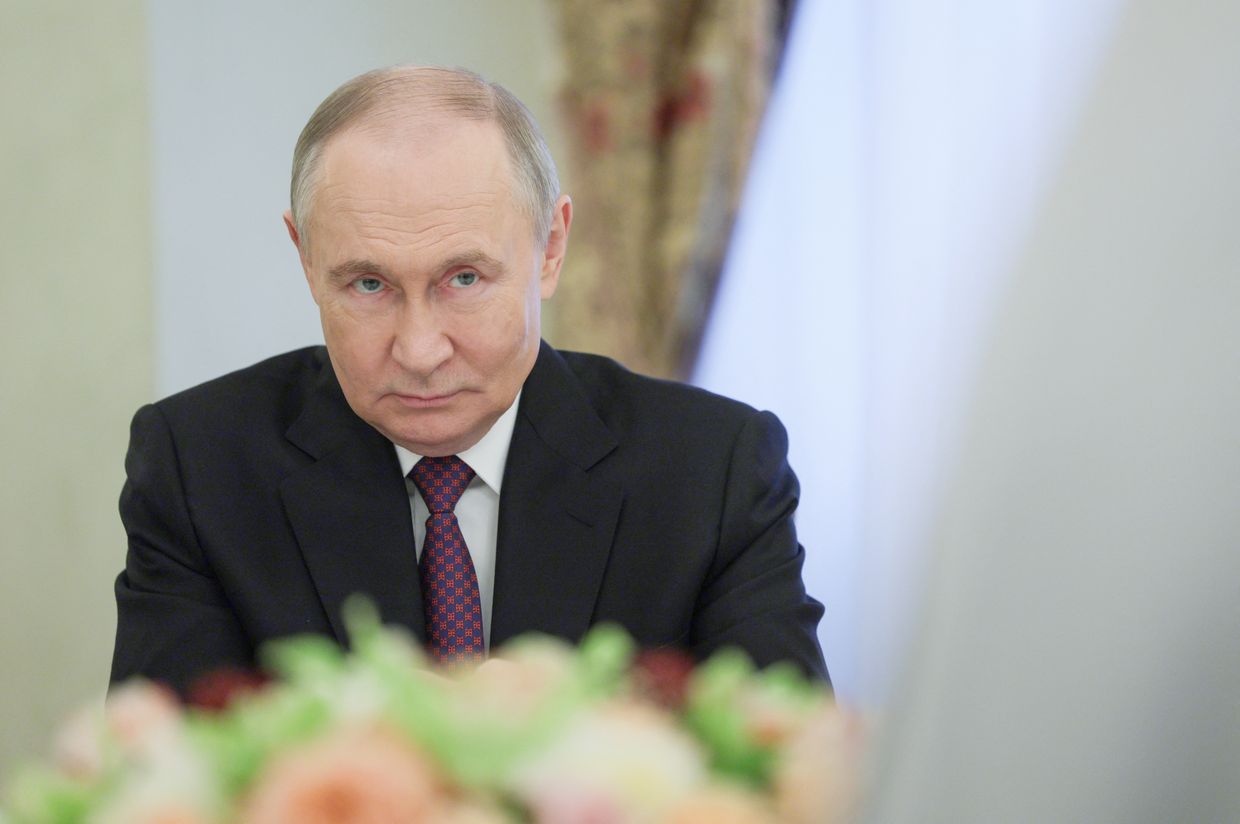
Putin Breaks Silence: Russia's Arsenal Falls Short in Manufacturing Crunch
2025-04-23 12:45:06
Manufacturing
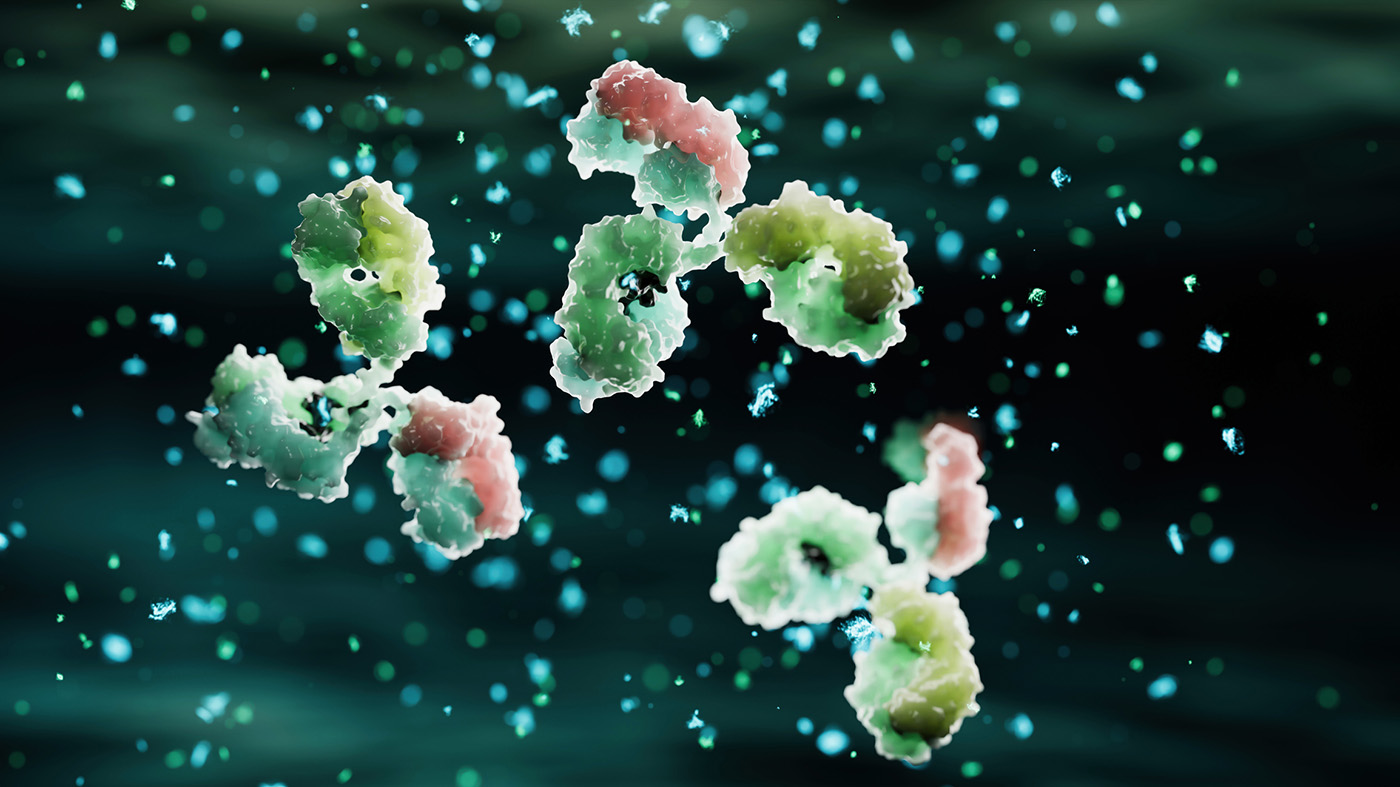
Speed Meets Science: How Next-Gen Sequencing is Revolutionizing Antibody Production
2025-03-07 23:48:58