Smart Factories Revolution: How AI is Rewriting the Future of Manufacturing
Manufacturing
2025-02-25 10:00:00Content
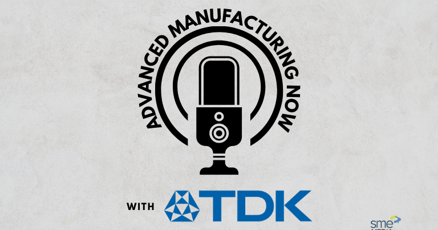
The Future of Manufacturing: How AI and Machine Health Monitoring Are Transforming Industry
In the rapidly evolving landscape of modern manufacturing, artificial intelligence and advanced machine health monitoring are driving a revolutionary transformation. We're witnessing an unprecedented shift from traditional reactive maintenance to a proactive, intelligent approach that promises to redefine industrial efficiency.
From Industry 4.0 to Industry 5.0: A Technological Leap
The journey from Industry 4.0 to Industry 5.0 represents more than just technological advancement—it's a paradigm shift where human creativity and machine intelligence converge. Advanced machine health monitoring systems are at the forefront of this transformation, offering unprecedented insights into equipment performance and potential vulnerabilities.
Predictive Maintenance: The Game-Changer
Imagine a manufacturing environment where machines can predict their own maintenance needs before a breakdown occurs. With AI-powered predictive maintenance, this is no longer a distant dream but an emerging reality. These intelligent systems analyze complex data patterns, detecting subtle anomalies that human observers might miss, ultimately preventing costly downtime and extending equipment lifespan.
Actionable Insights: Empowering Decision-Makers
Modern machine health monitoring goes beyond simple data collection. It provides actionable, strategic insights that enable managers to make informed decisions. Real-time analytics, machine learning algorithms, and sophisticated sensor technologies work in harmony to create a comprehensive understanding of industrial equipment performance.
The Human-Machine Collaboration
As we transition into Industry 5.0, the focus is not on replacing human workers but enhancing their capabilities. AI and advanced monitoring systems become collaborative tools, augmenting human expertise and driving innovation across manufacturing processes.
The future of manufacturing is intelligent, predictive, and remarkably efficient—a testament to the incredible potential of technological innovation.
The Digital Revolution: How Artificial Intelligence is Transforming Manufacturing Landscapes
In an era of unprecedented technological transformation, manufacturing stands at the precipice of a radical metamorphosis driven by artificial intelligence and advanced machine health monitoring technologies. The convergence of cutting-edge digital innovations is reshaping industrial paradigms, propelling traditional manufacturing processes into a new realm of efficiency, predictability, and intelligent automation.Unleashing the Power of Intelligent Manufacturing: Where Technology Meets Innovation
The Evolution of Machine Intelligence
Modern manufacturing is experiencing a profound technological renaissance, where artificial intelligence serves as the primary catalyst for unprecedented operational transformation. Traditional maintenance strategies, characterized by reactive interventions and manual inspections, are rapidly giving way to sophisticated predictive methodologies powered by advanced algorithmic systems. Machine learning algorithms now possess the extraordinary capability to analyze complex operational data streams, identifying subtle performance anomalies with remarkable precision. These intelligent systems can predict potential equipment failures weeks or even months before traditional diagnostic methods, enabling manufacturers to implement preemptive maintenance strategies that minimize downtime and optimize resource allocation.Predictive Maintenance: A Paradigm Shift in Industrial Operations
The integration of artificial intelligence into machine health monitoring represents a quantum leap in industrial maintenance philosophy. By leveraging sophisticated sensor technologies and real-time data analytics, manufacturers can now transition from reactive repair models to proactive performance optimization strategies. Sophisticated neural networks continuously analyze equipment performance metrics, creating comprehensive digital twins that simulate potential mechanical stress scenarios. These virtual representations allow engineers to anticipate potential failure points, schedule strategic maintenance interventions, and dramatically reduce unexpected operational disruptions.From Industry 4.0 to Industry 5.0: The Human-Machine Collaboration
The technological trajectory is progressively moving beyond traditional automation towards a more nuanced human-machine collaborative ecosystem. Industry 5.0 emphasizes not just technological efficiency but also the strategic integration of human creativity and machine intelligence. Advanced monitoring systems now provide actionable insights that empower human decision-makers, transforming raw data into strategic intelligence. Operators can access comprehensive dashboards that offer real-time performance analytics, enabling more informed and agile operational decisions.Economic and Operational Implications of AI-Driven Manufacturing
The economic potential of intelligent manufacturing technologies is staggering. Companies implementing comprehensive AI-powered monitoring systems can potentially reduce maintenance costs by up to 40%, increase equipment reliability by 25%, and improve overall operational efficiency by significant margins. These technological investments are not merely about cost reduction but represent fundamental reimaginations of industrial productivity. By creating more resilient, adaptive, and intelligent manufacturing ecosystems, organizations can develop competitive advantages that transcend traditional operational boundaries.Technological Infrastructure and Implementation Challenges
While the promise of AI-driven manufacturing is immense, successful implementation requires sophisticated technological infrastructure and strategic organizational commitment. Companies must invest in robust data collection mechanisms, advanced computational resources, and comprehensive training programs to fully leverage these transformative technologies. Cybersecurity considerations also become paramount, as increasingly interconnected systems demand rigorous protection against potential digital vulnerabilities. Manufacturers must develop holistic strategies that balance technological innovation with robust security protocols.Future Horizons: Emerging Trends in Intelligent Manufacturing
The future of manufacturing will be characterized by increasingly autonomous, self-optimizing systems that can adapt in real-time to changing operational conditions. Emerging technologies like edge computing, advanced machine learning models, and quantum computational approaches promise to further accelerate the intelligent manufacturing revolution. As artificial intelligence continues to evolve, we can anticipate manufacturing environments that are not just responsive but genuinely predictive, creating unprecedented levels of operational efficiency and strategic adaptability.RELATED NEWS
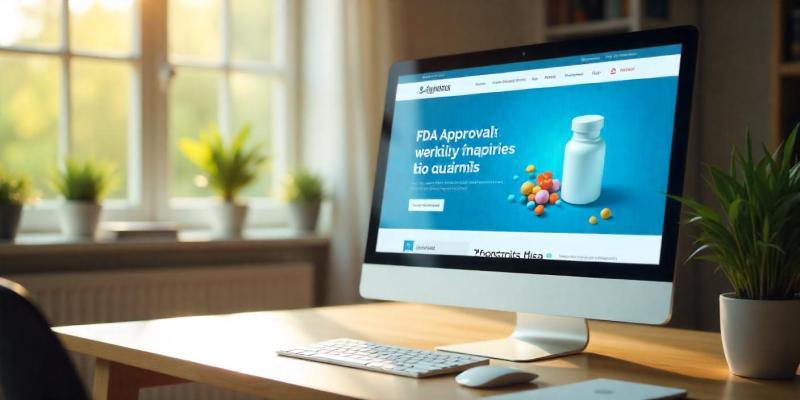
Pharma Manufacturing Titans Redraw Global Supply Map: Billion-Dollar Deals Spark Industry Transformation
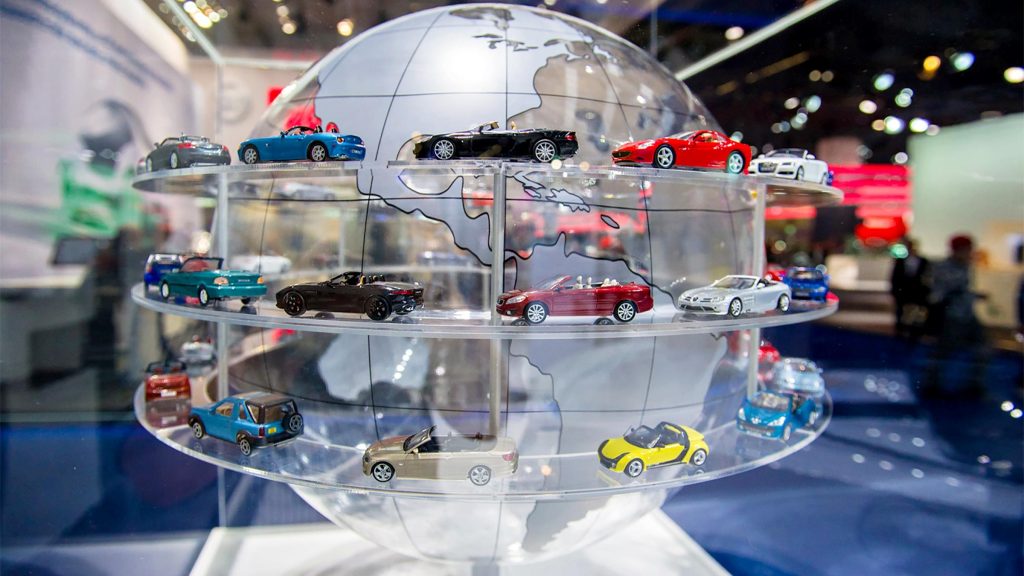
Tariff Tangle: How US Auto Taxes Could Backfire on Detroit and Global Car Giants
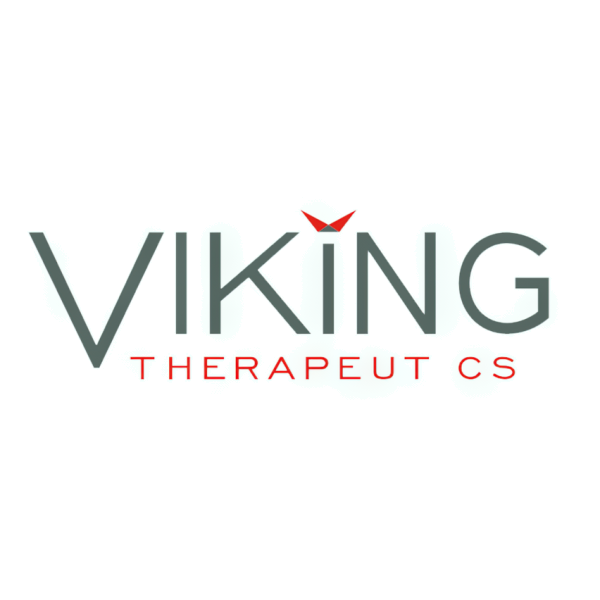