3D Printing's Crossroads: Can the Additive Manufacturing Industry Survive the 2025 Challenge?
Manufacturing
2025-03-02 23:01:42Content
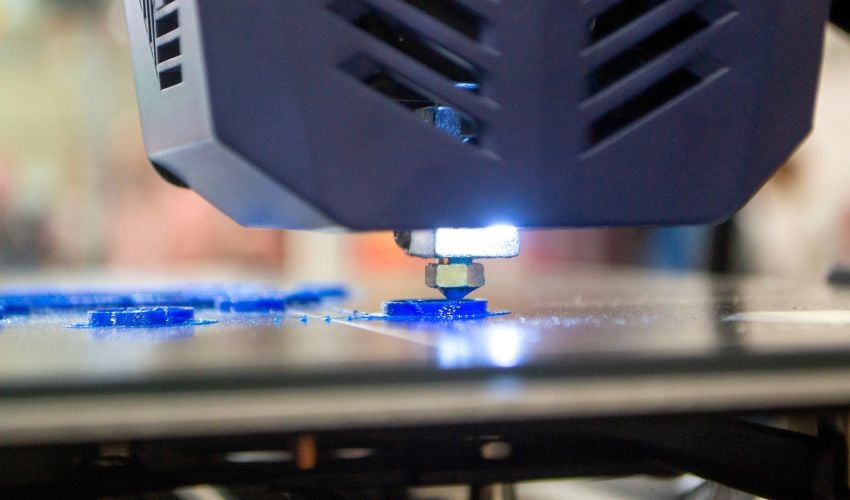
Additive Manufacturing: Charting a Course to Hope in 2025
As we stand on the cusp of technological transformation, the world of additive manufacturing pulses with potential and promise. What was once a niche technology is rapidly evolving into a game-changing industrial solution that could reshape how we design, produce, and conceptualize manufacturing.
The landscape of 3D printing and advanced manufacturing is no longer about mere experimentation—it's about strategic innovation. From aerospace to healthcare, industries are discovering that additive manufacturing offers more than just prototype creation; it represents a fundamental reimagining of production processes.
Key challenges remain, of course. Cost efficiency, material limitations, and scalability continue to test the boundaries of this technology. Yet, the momentum is undeniable. Emerging technologies are addressing these constraints, bringing us closer to a future where complex, customized components can be printed with unprecedented speed and precision.
As we look toward 2025, the horizon for additive manufacturing looks increasingly bright. Technological advancements, reduced production costs, and growing industrial acceptance suggest we're not just witnessing incremental progress—we're experiencing a potential industrial revolution.
The journey continues, and hope is not just a distant dream, but an emerging reality.
Additive Manufacturing in 2025: A Transformative Journey of Innovation and Potential
The landscape of manufacturing is on the brink of a revolutionary transformation, with additive manufacturing poised to redefine how industries approach production, design, and innovation. As we stand at the cusp of technological breakthrough, the potential of 3D printing and advanced manufacturing techniques promises to reshape our understanding of what's possible in industrial and creative domains.Unleashing the Future: Additive Manufacturing's Breakthrough Potential
The Technological Renaissance of Manufacturing
The additive manufacturing sector is experiencing an unprecedented wave of technological innovation that transcends traditional manufacturing limitations. Unlike conventional subtractive methods, 3D printing enables unprecedented design flexibility, material optimization, and complex geometric configurations that were previously impossible. Engineers and designers are now empowered to create intricate structures with minimal material waste, revolutionizing everything from aerospace components to medical implants. Cutting-edge research institutions and forward-thinking corporations are investing heavily in advanced additive manufacturing technologies. These investments are driving exponential improvements in printing speed, material diversity, and precision. Emerging technologies like multi-material printing and nano-scale fabrication are expanding the boundaries of what can be manufactured, promising solutions to complex engineering challenges.Economic and Industrial Implications
The economic landscape of manufacturing is undergoing a profound metamorphosis driven by additive manufacturing technologies. Traditional supply chains are being disrupted as companies recognize the potential for localized, on-demand production. This shift not only reduces transportation costs and inventory management complexities but also enables unprecedented customization and rapid prototyping. Industries ranging from automotive and aerospace to healthcare and consumer electronics are integrating additive manufacturing into their core production strategies. The ability to produce complex, lightweight components with reduced material consumption is creating significant competitive advantages. Moreover, the sustainability potential of these technologies is attracting increased attention from environmentally conscious organizations seeking to minimize their carbon footprint.Technological Challenges and Breakthrough Opportunities
Despite remarkable progress, additive manufacturing still confronts significant technological challenges. Material limitations, production scalability, and cost-effectiveness remain critical areas of ongoing research and development. Researchers are exploring advanced materials like high-performance polymers, metal alloys, and ceramic composites that can withstand extreme conditions while maintaining structural integrity. Artificial intelligence and machine learning are emerging as powerful tools in optimizing additive manufacturing processes. Predictive algorithms can now simulate and refine complex manufacturing parameters, reducing trial-and-error approaches and enhancing overall production efficiency. These technological convergences are creating unprecedented opportunities for innovation across multiple sectors.Global Market Dynamics and Future Projections
The global additive manufacturing market is projected to experience exponential growth, with estimates suggesting a potential market value exceeding $50 billion by 2025. Emerging economies are rapidly adopting these technologies, recognizing their potential to leapfrog traditional manufacturing constraints. Collaborative international research initiatives are accelerating technological development, creating a global ecosystem of innovation. Geopolitical dynamics are also influencing the additive manufacturing landscape, with nations investing strategically in research and development. The ability to rapidly prototype and produce critical components domestically is becoming increasingly important in an era of complex global supply chains and potential disruptions.Human Capital and Skills Transformation
The rise of additive manufacturing is fundamentally reshaping workforce skills and educational paradigms. Universities and technical institutions are developing specialized programs focusing on advanced manufacturing technologies, preparing a new generation of engineers and designers equipped to leverage these transformative tools. Interdisciplinary collaboration is becoming crucial, with professionals from materials science, computer engineering, design, and manufacturing working together to push technological boundaries. This holistic approach is generating innovative solutions that transcend traditional disciplinary limitations.RELATED NEWS
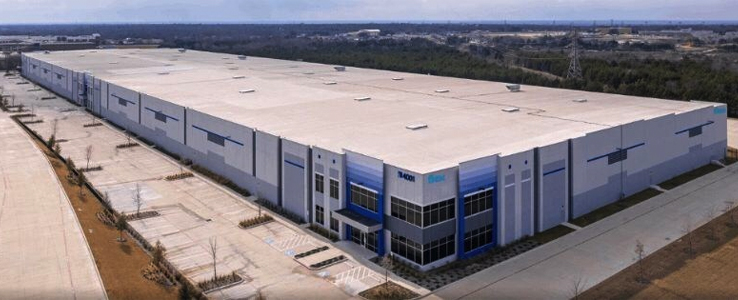
Manufacturing Boost: Flex Unveils Cutting-Edge Dallas Production Hub
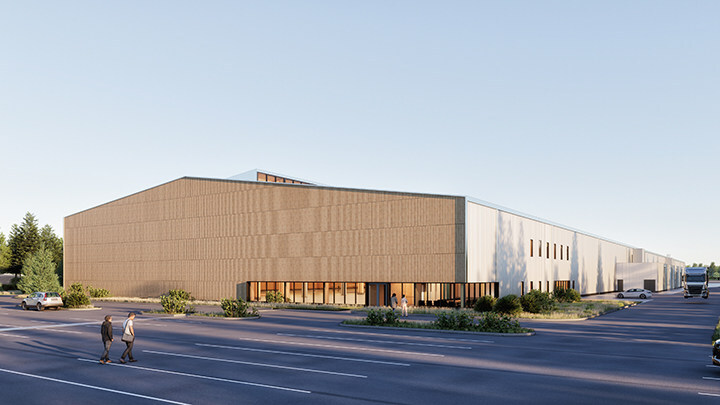