From Factory Floor to Future: 5 Game-Changing Strategies for Smart Manufacturing Revolution
Manufacturing
2025-04-17 08:54:59Content
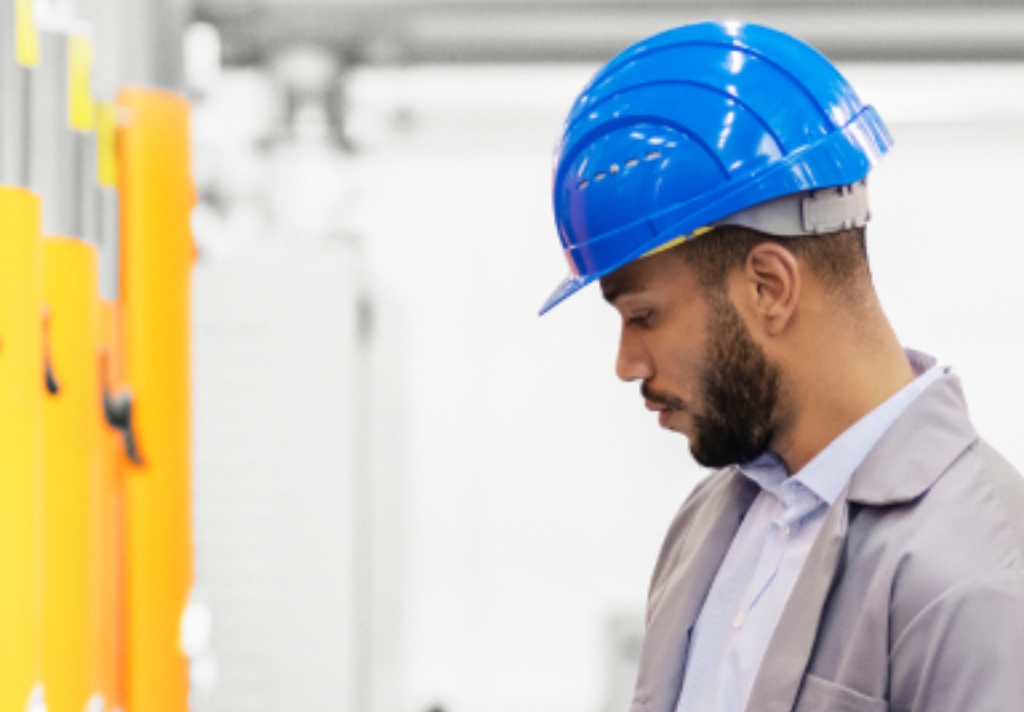
Unlocking the Power of Connected Manufacturing: Navigating the Path to Digital Transformation
In today's rapidly evolving industrial landscape, connected manufacturing stands as a beacon of innovation and efficiency. While the potential benefits are undeniably compelling, Verizon acknowledges that the journey to digital transformation is far from straightforward.
Modern manufacturers are increasingly recognizing the transformative potential of connected technologies. These advanced systems promise to revolutionize production processes, enhance operational visibility, and drive unprecedented levels of productivity. However, the road to implementation is often complex and demands careful strategic planning.
The complexity of digital transformation stems from multiple factors. Organizations must carefully integrate new technologies with existing infrastructure, retrain workforce capabilities, and develop robust data management strategies. It's not simply about adopting new tools, but fundamentally reimagining manufacturing operations.
Verizon emphasizes that successful connected manufacturing requires a holistic approach. Companies must:
• Invest in cutting-edge connectivity solutions
• Develop comprehensive digital strategies
• Foster a culture of continuous innovation
• Prioritize cybersecurity and data protection
While the path may be challenging, the potential rewards are substantial. Connected manufacturing offers manufacturers the ability to optimize production, reduce downtime, improve quality control, and create more agile, responsive business models.
The key is patience, strategic investment, and a commitment to ongoing digital evolution. As technology continues to advance, those who embrace connected manufacturing will be best positioned to thrive in an increasingly competitive global marketplace.
Digital Revolution: Transforming Manufacturing Through Intelligent Connectivity
In an era of unprecedented technological advancement, manufacturing industries are experiencing a profound metamorphosis driven by interconnected digital technologies. The landscape of industrial production is rapidly evolving, challenging traditional paradigms and introducing sophisticated strategies that redefine operational efficiency, productivity, and competitive advantage.Unleashing the Power of Smart Manufacturing: Where Innovation Meets Precision
The Technological Convergence in Modern Manufacturing
The contemporary manufacturing ecosystem represents a complex intersection of advanced technologies, where intelligent systems communicate seamlessly across multiple platforms. Cutting-edge sensors, artificial intelligence, and robust network infrastructures are transforming production environments from static mechanical spaces into dynamic, responsive intelligent networks. Manufacturers are no longer constrained by traditional linear processes but can now leverage real-time data analytics to optimize every aspect of their operational workflow. Sophisticated machine learning algorithms enable predictive maintenance strategies, allowing organizations to anticipate potential equipment failures before they occur. By continuously monitoring machinery performance metrics, companies can dramatically reduce unexpected downtime, minimize maintenance costs, and extend the operational lifespan of critical industrial assets.Strategic Implementation of Connected Manufacturing Technologies
Implementing connected manufacturing technologies requires a holistic and strategic approach that transcends mere technological adoption. Organizations must develop comprehensive digital transformation roadmaps that align technological investments with overarching business objectives. This involves creating robust digital infrastructure, training workforce personnel, and cultivating a culture of continuous innovation and technological adaptability. Enterprise-wide digital integration demands significant cultural and organizational shifts. Successful implementation necessitates breaking down traditional departmental silos, encouraging cross-functional collaboration, and developing agile methodological frameworks that can rapidly respond to emerging technological trends and market dynamics.Economic and Operational Implications of Digital Manufacturing
The economic potential of connected manufacturing extends far beyond incremental efficiency improvements. By leveraging advanced data analytics and intelligent automation, organizations can unlock unprecedented levels of operational transparency, resource optimization, and strategic decision-making capabilities. Manufacturers embracing digital transformation can achieve substantial competitive advantages, including reduced operational costs, enhanced product quality, accelerated time-to-market, and improved customer satisfaction. The ability to collect, analyze, and act upon real-time production data enables organizations to create more responsive, flexible, and customer-centric manufacturing ecosystems.Cybersecurity and Risk Management in Connected Environments
As manufacturing systems become increasingly interconnected, robust cybersecurity frameworks become paramount. The proliferation of digital technologies introduces complex security challenges that require sophisticated, multi-layered protection strategies. Organizations must develop comprehensive risk management protocols that safeguard critical infrastructure against potential cyber threats while maintaining operational flexibility. Advanced encryption technologies, continuous monitoring systems, and proactive threat detection mechanisms are essential components of a comprehensive industrial cybersecurity strategy. Manufacturers must invest in ongoing employee training programs and develop resilient technological architectures capable of adapting to emerging security challenges.Future Trajectory of Intelligent Manufacturing Ecosystems
The future of manufacturing lies in creating increasingly intelligent, adaptive, and self-optimizing production environments. Emerging technologies such as edge computing, advanced robotics, and quantum computing are poised to revolutionize industrial production methodologies, enabling unprecedented levels of precision, efficiency, and innovation. As technological capabilities continue to expand, manufacturers will transition from reactive operational models to predictive, proactive systems that can autonomously adapt to changing market conditions, customer demands, and technological landscapes.RELATED NEWS
Manufacturing
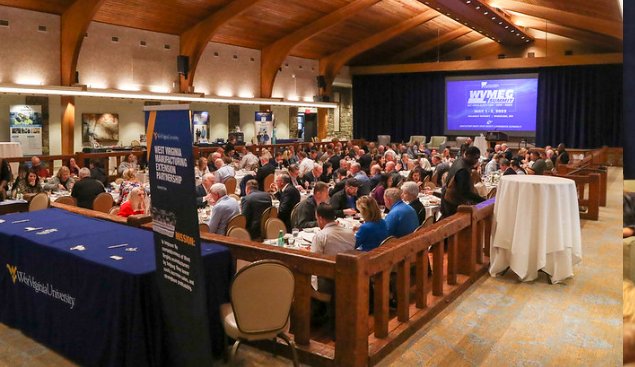
Powering Tomorrow: Industry Leaders Converge at Oglebay for 2025 Manufacturing and Energy Revolution Summit
2025-05-05 11:47:45
Manufacturing
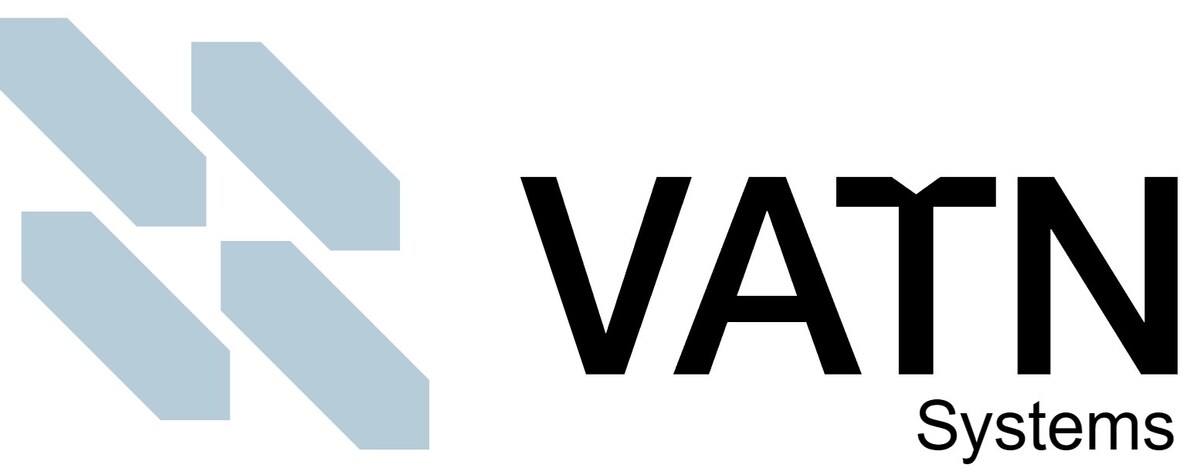
Underwater Robotics Revolution: Vatn Systems and Palantir Join Forces to Supercharge Defense Drone Production
2025-04-16 12:02:00
Manufacturing
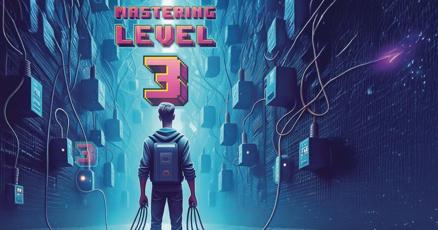
Breaking Barriers: The Insider's Guide to Conquering Level 3 Like a Pro
2025-04-02 15:21:00