Drone Revolution: How 3D Printing is Transforming Unmanned Aerial Vehicle Engineering
Manufacturing
2025-04-15 19:43:31Content
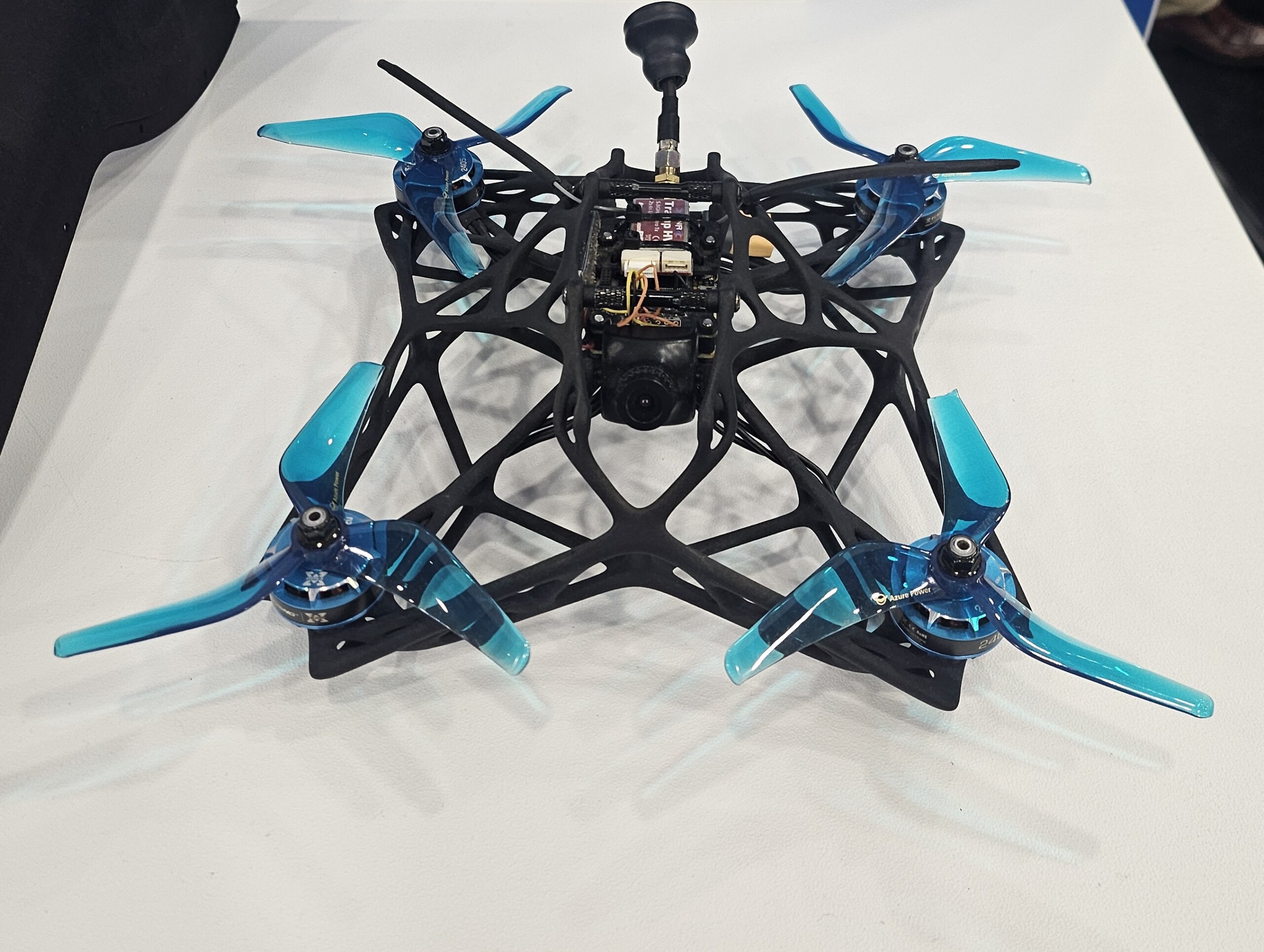
The revolutionary world of 3D printing is transforming manufacturing through three powerful capabilities: lightweighting, topology optimization, and advanced digital workflows. This cutting-edge technology is breaking traditional design barriers and enabling engineers and designers to create increasingly sophisticated and efficient components.
Lightweighting has become a game-changing approach across industries like aerospace, automotive, and robotics. By using 3D printing, manufacturers can now design intricate structures that dramatically reduce material weight without compromising structural integrity. Complex geometries that were once impossible to produce can now be realized with precision and minimal mass.
Topology optimization takes design innovation even further. This computational technique allows engineers to mathematically analyze and optimize part designs, creating structures that maximize performance while minimizing material usage. 3D printing makes these mathematically complex designs physically achievable, pushing the boundaries of what's possible in product development.
Digital workflows powered by 3D printing are streamlining the entire product design and manufacturing process. From rapid prototyping to on-demand production, these integrated digital technologies enable faster iterations, reduced waste, and more flexible manufacturing strategies. Engineers can now move seamlessly from digital concept to physical reality with unprecedented speed and accuracy.
As 3D printing technologies continue to evolve, they promise to revolutionize how we conceive, design, and produce everything from microscopic medical devices to massive industrial components, marking a new era of manufacturing innovation.
Revolutionizing Manufacturing: The Transformative Power of 3D Printing Technologies
In the rapidly evolving landscape of modern manufacturing, technological innovations are reshaping how industries conceptualize, design, and produce complex components. At the forefront of this industrial revolution stands 3D printing, a groundbreaking technology that is fundamentally transforming traditional manufacturing paradigms and pushing the boundaries of engineering possibilities.Unleashing Unprecedented Design Freedom and Engineering Potential
The Digital Manufacturing Renaissance
Advanced additive manufacturing technologies are dramatically reimagining the manufacturing ecosystem. Unlike traditional subtractive manufacturing methods, 3D printing enables engineers and designers to create intricate geometries that were previously impossible or prohibitively expensive to produce. The technology allows for unprecedented design complexity, enabling the creation of lightweight, structurally optimized components that challenge conventional manufacturing limitations. The computational power behind topology optimization algorithms has become a game-changing companion to 3D printing technologies. These sophisticated mathematical models analyze structural requirements and material distribution, generating designs that maximize performance while minimizing material usage. Engineers can now develop components that are not just lighter, but also stronger and more efficient than their traditionally manufactured counterparts.Computational Design and Digital Workflows
Modern 3D printing workflows integrate advanced computational design tools that transform how engineers conceptualize and realize complex structures. Sophisticated software platforms enable real-time simulation, allowing designers to predict and optimize component performance before physical production. This digital-first approach reduces prototyping costs, accelerates development cycles, and minimizes material waste. The integration of artificial intelligence and machine learning algorithms further enhances these digital workflows. By analyzing vast datasets of material properties, structural performance, and manufacturing constraints, these intelligent systems can suggest optimal design configurations that human engineers might overlook. This symbiosis between human creativity and computational intelligence is pushing the boundaries of what's achievable in manufacturing.Material Innovation and Performance Engineering
The evolution of 3D printing extends far beyond geometric flexibility, encompassing remarkable material science advancements. Contemporary additive manufacturing technologies support an expansive range of materials, from advanced polymers and metal alloys to ceramic composites and hybrid materials with tailored mechanical properties. Researchers and engineers are developing increasingly sophisticated material formulations that can be precisely deposited layer by layer, enabling the creation of components with gradient properties, embedded functionalities, and unprecedented structural characteristics. These material innovations are opening new frontiers in aerospace, medical devices, automotive engineering, and numerous other high-performance industries.Sustainability and Economic Transformation
3D printing represents more than a technological breakthrough; it's a sustainable manufacturing paradigm. By enabling precise material deposition and reducing waste, additive manufacturing significantly decreases the environmental footprint of industrial production. The ability to produce complex components with minimal material consumption translates into substantial economic and ecological benefits. The localized production capabilities of 3D printing are reshaping global supply chains. Companies can now manufacture components on-demand, reducing inventory costs, minimizing transportation emissions, and creating more resilient, adaptable manufacturing ecosystems. This shift towards decentralized, digital manufacturing represents a fundamental reimagining of industrial production strategies.Future Horizons and Emerging Possibilities
As 3D printing technologies continue to mature, their potential applications seem boundless. From biomedical engineering, where custom prosthetics and tissue scaffolds can be precisely fabricated, to space exploration, where complex components can be printed on-site, the technology is poised to revolutionize multiple domains. Emerging research suggests we are merely scratching the surface of additive manufacturing's transformative potential. Interdisciplinary collaborations between materials scientists, computational engineers, and design experts are continuously expanding the technological frontiers, promising even more remarkable innovations in the years to come.RELATED NEWS
Manufacturing
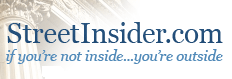
Manufacturing Revolution: Saint-Gobain's Bold Training Initiative Reshapes Industrial Workforce
2025-03-17 12:00:00
Manufacturing
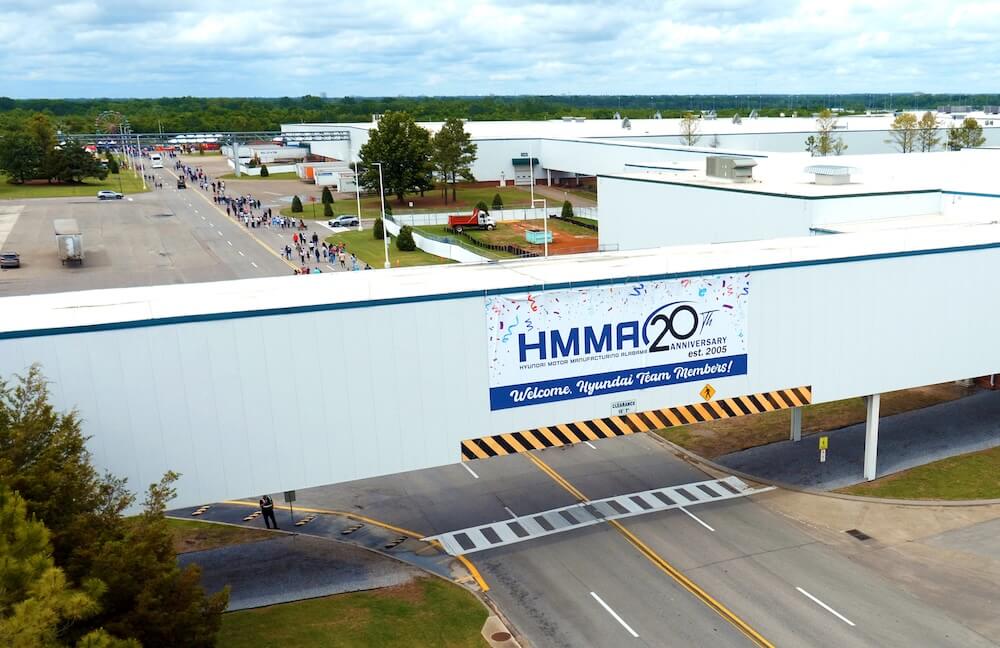
Leadership Shift: Hyundai Taps New Chief to Steer Manufacturing Future
2025-05-06 14:17:53