Revolutionary 6D Manufacturing: APES Unveils Groundbreaking Matrix Modular Adaptive Platform
Manufacturing
2025-04-09 15:49:40Content

Revolutionizing Manufacturing: A Platform That Transforms Production Flexibility
Imagine a cutting-edge manufacturing solution that breaks traditional production barriers. Our innovative platform empowers businesses with unprecedented flexibility, offering three key capabilities that redefine modern manufacturing:
• Mass Customization: Seamlessly adapt production to unique customer requirements, creating personalized products at scale
• Parallel Part Production: Maximize efficiency by simultaneously manufacturing multiple components, dramatically reducing lead times
• Dynamic Task Management: Intelligently allocate resources, optimize workflows, and respond instantly to changing production demands
By integrating advanced technologies and intelligent design, this platform enables manufacturers to transform complex production challenges into streamlined, responsive manufacturing processes. Whether you're a small workshop or a large industrial enterprise, the solution provides the agility and precision needed to stay competitive in today's rapidly evolving market.
Revolutionary Matrix6D: Transforming Manufacturing Through Adaptive 3D Printing Technology
In the rapidly evolving landscape of advanced manufacturing, groundbreaking technologies are continuously reshaping how industries conceptualize, design, and produce complex components. The emergence of adaptive 3D printing platforms represents a paradigm shift that promises to revolutionize traditional manufacturing methodologies, offering unprecedented flexibility and efficiency.Unleashing Manufacturing Potential: Where Innovation Meets Precision
The Technological Breakthrough of Adaptive Manufacturing
The Matrix6D platform represents a quantum leap in manufacturing technology, fundamentally reimagining how complex components are conceived and produced. Unlike traditional manufacturing processes that rely on rigid, predetermined workflows, this innovative system introduces unprecedented dynamism and adaptability. By integrating advanced algorithmic intelligence with cutting-edge 3D printing capabilities, the platform enables manufacturers to transcend conventional production limitations. Engineers and designers can now leverage a system that responds in real-time to intricate design requirements, seamlessly adjusting parameters and production strategies. The platform's sophisticated neural network continuously analyzes production metrics, optimizing each manufacturing cycle with remarkable precision. This intelligent approach ensures that every printed component meets exacting specifications while minimizing material waste and production time.Customization at Scale: Redefining Production Paradigms
Mass customization has long been an elusive goal for manufacturers, traditionally hindered by inflexible production infrastructures. The Matrix6D platform shatters these constraints, providing an ecosystem where personalized, high-complexity components can be produced efficiently and economically. By implementing parallel production capabilities, manufacturers can simultaneously generate multiple unique parts without compromising overall production velocity. The system's adaptive algorithms enable rapid reconfiguration of manufacturing parameters, allowing seamless transitions between different design specifications. This flexibility empowers industries ranging from aerospace and medical technology to automotive engineering to create highly specialized components with unprecedented ease. Each production run becomes a dynamic, intelligent process that adapts and evolves in real-time.Dynamic Task Management: The Intelligent Production Ecosystem
Central to the Matrix6D's revolutionary approach is its sophisticated task management infrastructure. Traditional manufacturing systems often struggle with complex, multi-stage production processes, experiencing bottlenecks and inefficiencies. This platform introduces an intelligent orchestration mechanism that dynamically allocates resources, balances workloads, and optimizes production workflows. The system's machine learning algorithms continuously analyze production data, identifying potential optimization opportunities and preemptively addressing potential challenges. By integrating predictive maintenance protocols and real-time performance monitoring, manufacturers can achieve unprecedented levels of operational reliability and efficiency. Each production cycle becomes an opportunity for continuous improvement, with the platform learning and adapting from every interaction.Sustainability and Economic Implications
Beyond technological innovation, the Matrix6D platform carries profound sustainability implications. By minimizing material waste, reducing energy consumption, and enabling more localized production strategies, this technology represents a significant step towards more environmentally responsible manufacturing practices. The ability to produce complex components with minimal raw material input translates into substantial economic and ecological benefits. Manufacturers adopting this technology can expect reduced production costs, shorter time-to-market cycles, and enhanced product complexity. The platform's ability to produce intricate, high-precision components opens new frontiers in industries demanding exceptional engineering tolerances, such as medical device manufacturing, aerospace engineering, and advanced robotics.RELATED NEWS
Manufacturing
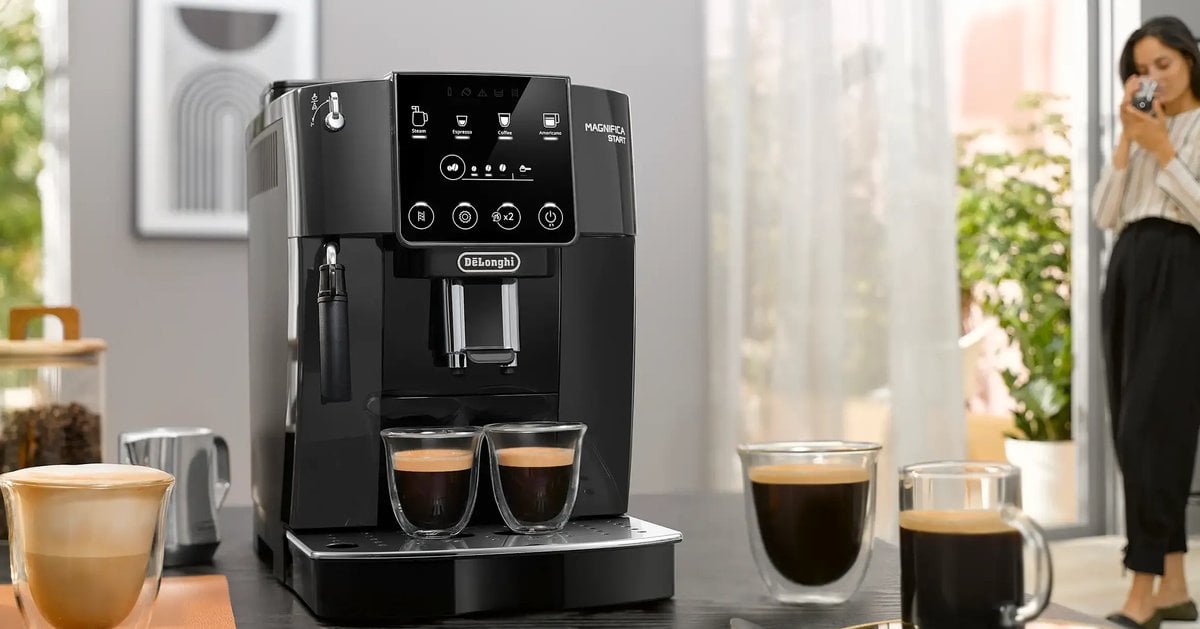
Supply Chain Revolution: De'Longhi Partners with Encompass to Supercharge Manufacturing Efficiency
2025-03-31 08:08:51
Manufacturing
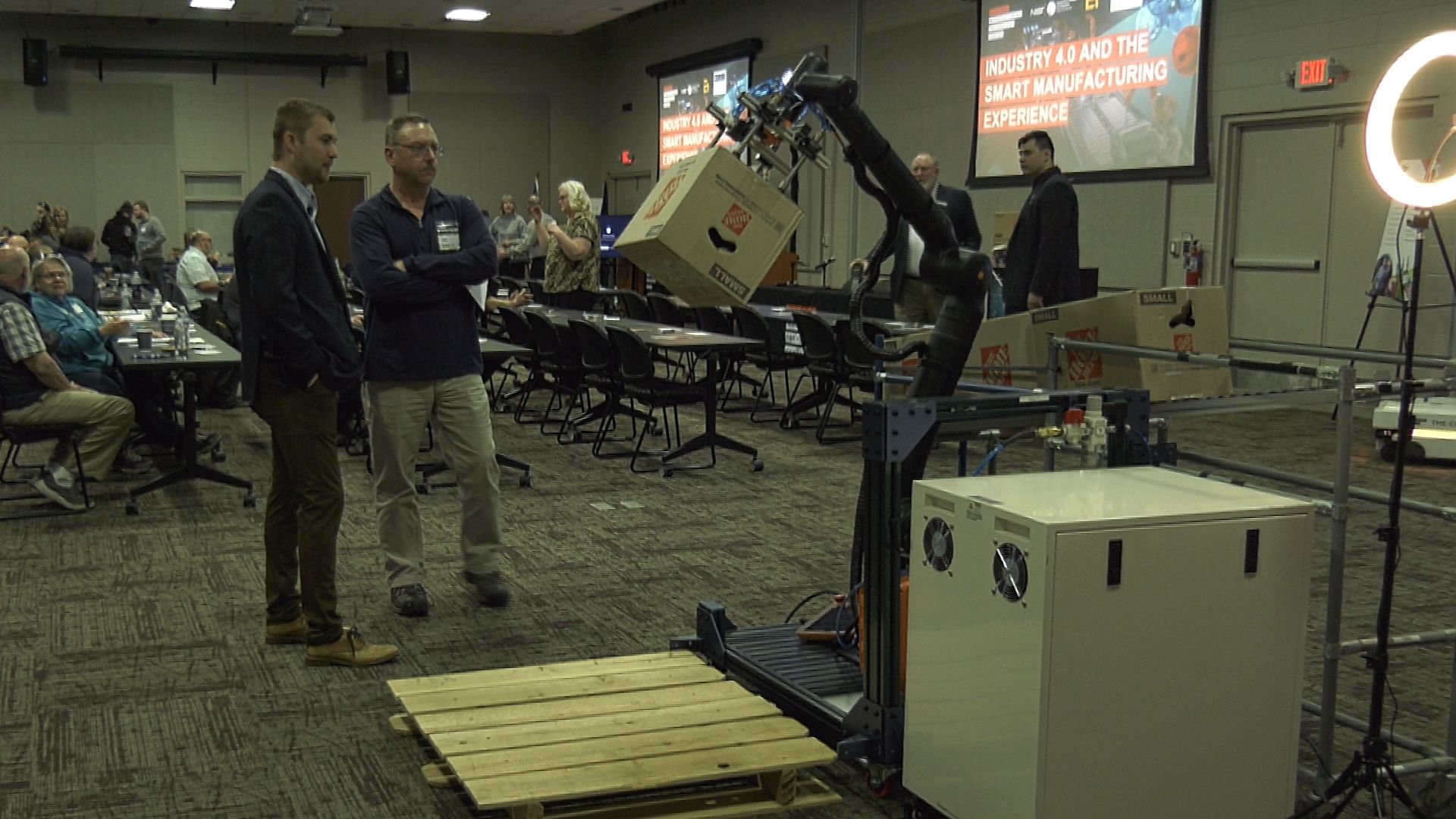
Future Factories Unveiled: Cutting-Edge Tech Transforms Manufacturing Landscape
2025-04-22 20:26:55
Manufacturing
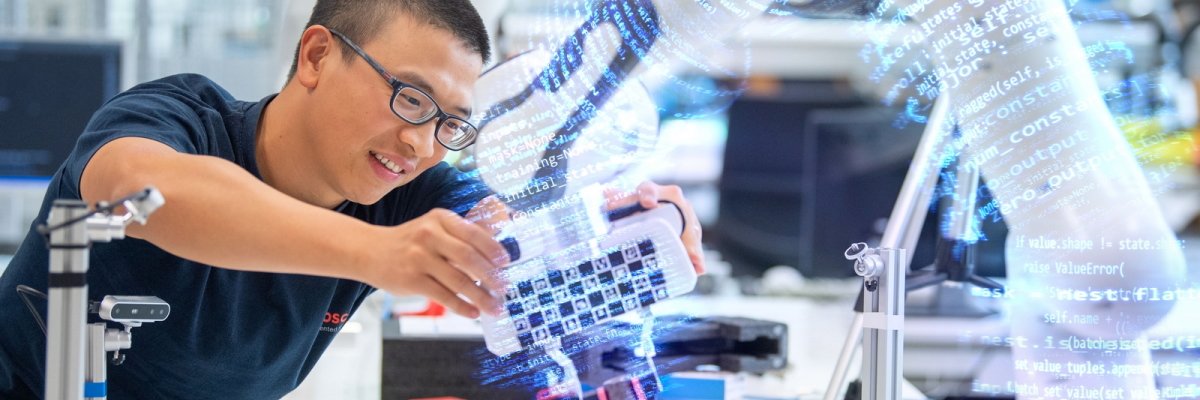
Beyond Automation: How Industry 5.0 is Reshaping the Future of Manufacturing
2025-02-26 05:45:00